CNC machining is best for premium, low-volume acetate eyewear, offering superior aesthetic detail and design freedom that justifies high margins. Injection molding is ideal for high-volume, accessible premium lines, providing scalability and lower per-unit costs once the significant initial mold investment is amortized. The right choice depends entirely on your brand strategy and target market.
Both processes deliver acetate eyewear, but they target vastly different market segments. CNC machining creates artisanal luxury pieces with superior material integrity, while injection molding enables scalable manufacturing for accessible premium lines. Understanding these distinctions allows you to align your production method with your brand strategy and revenue goals.
The Strategic Imperative: Aligning Production to Brand Position
Your manufacturing method is a direct reflection of your brand’s core strategy. This choice dictates your price point, target audience, and ultimately, your path to profitability. Each approach creates a distinct value proposition that attracts different consumers and supports different revenue models.
The Luxury Play: CNC Machining for High-Margin Collections
Observation/Finding: CNC machining positions your acetate eyewear as artisanal products that command premium prices. The subtractive manufacturing process leverages the full aesthetic potential of premium materials like Mazzucchelli acetate blocks.
Strategic Implication: This approach supports luxury brand narratives because cutting from a solid block preserves the rich, deep color layers of laminated acetate, creating visual depth impossible to achieve through injection molding.
Competitive/Financial Outcome: This superior quality justifies retail prices 3-5 times higher than injection-molded equivalents. Key Metric: This translates to gross margins exceeding 70% for premium collections, appealing to affluent consumers who value craftsmanship and authenticity.
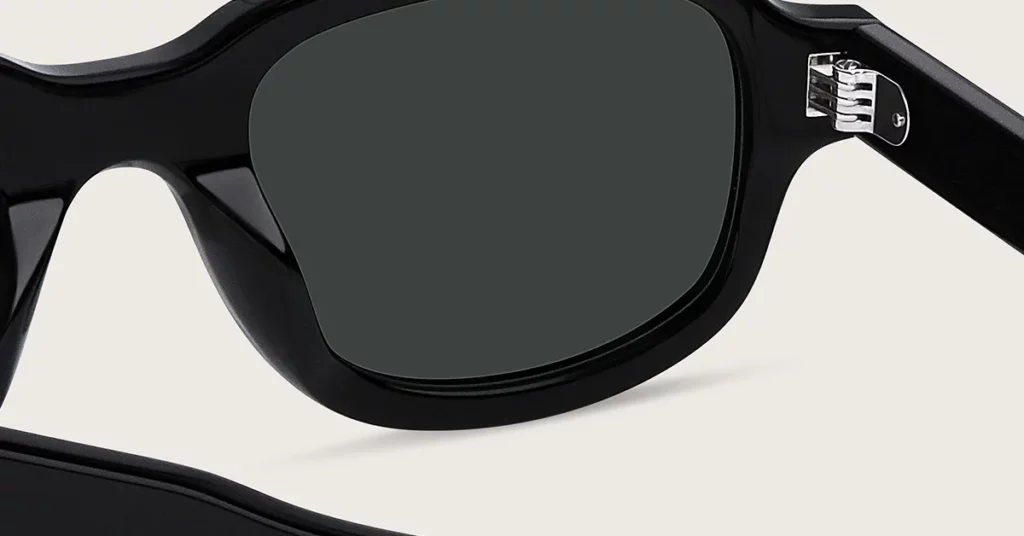
The Scalability Play: Injection Molding for High-Volume Lines
Observation/Finding: Injection molding democratizes premium acetate by enabling mass production at competitive price points. It utilizes pelletized acetate processed through high-pressure systems.
Strategic Implication: While sacrificing some of the aesthetic complexity of block acetate, this approach delivers consistent quality across thousands of units. This makes premium materials like acetate accessible to broader market segments.
Competitive/Financial Outcome: Once tooling investments are amortized over 1,000+ units, per-unit costs for injection-molded frames can drop to $8-$15, compared to $30-$60 for CNC. This supports distribution through major retail chains and online platforms.
The Diversification Play: A Hybrid Strategy for Tiered Portfolios
Observation/Finding: Leading manufacturers now employ both methods to serve multiple market segments simultaneously. This hybrid approach maximizes revenue by capturing both luxury and volume opportunities within a single brand portfolio.
Strategic Implication: You can establish brand credibility with low-volume, high-margin CNC-machined signature collections. Then, you can achieve market penetration and volume growth with injection-molded lines for proven, popular designs.
Competitive/Financial Outcome: This tiered strategy minimizes risk. Best Practice: Use CNC for prototyping and market testing before committing capital to high-volume injection molding tools, maximizing learning while protecting your investment.
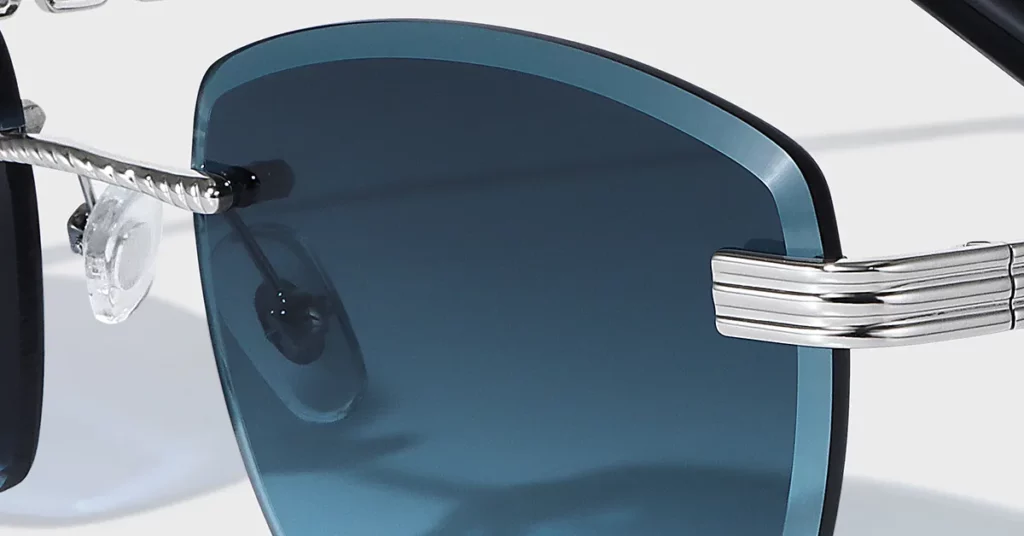
Calculating Total Cost of Ownership: A B2B Analysis
You must analyze the total cost of ownership, not just the per-unit price. Each method presents a different investment profile and risk level.
Cost Component | CNC Machining | Injection Molding |
Initial Tooling Investment | $500 – $2,000 | $5,000 – $50,000 |
Per-Unit Material Cost | $15 – $30 | $3 – $8 |
Labor Cost per Unit | $20 – $40 | $1 – $3 |
Break-Even Volume | 50 – 200 units | 1,000 – 5,000 units |
Design Change Cost | $0 – $500 | $2,000 – $15,000 |
Critical Warning: The high initial tooling investment for injection molding creates significant financial risk for unproven designs or uncertain demand. CNC machining’s flexibility provides superior risk management for new product introductions.
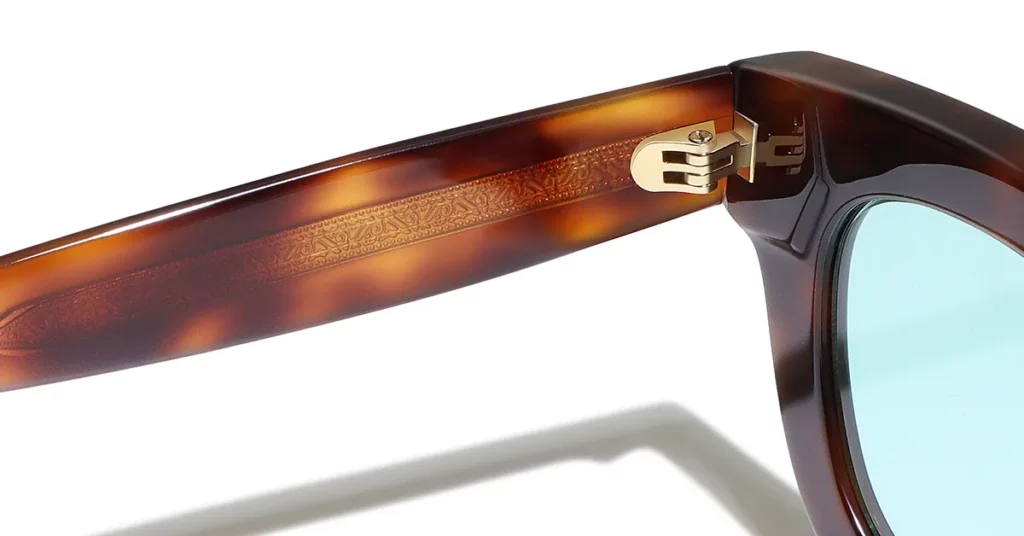
The CNC Machining Playbook: Quality, Detail, and Exclusivity
CNC machining is the pinnacle of precision acetate processing, delivering uncompromising quality while maintaining the design flexibility essential for premium eyewear brands.
The Subtractive Process: From Block to Frame
The process begins with exceptional raw materials. You must source fully cured acetate blocks that have undergone proper stabilization to prevent warping.
- The Material: Premium CNC machining requires solid acetate blocks, often from suppliers like Mazzucchelli. These blocks are laminated and cured under hydraulic pressure to eliminate air bubbles and ensure consistent density.
Definition: Curing is the chemical hardening process where acetate achieves final stability through controlled temperature and pressure.
- The Workflow: The process translates digital designs into physical frames. CAM software converts 3D models into G-code instructions that control multi-axis milling machines with tolerances as tight as ±0.005mm. This precision ensures perfect frame geometry and lens groove alignment.
- The Finish: Surface finishing transforms machined parts into polished luxury products. This involves a multi-day tumbling process followed by manual hand-polishing to achieve a lustrous, smooth surface. Tumbling operations span 72-120 hours using specialized media like wood chips and polishing compounds.
Critical Warning: Excessive tumbling can round sharp edges and compromise fit tolerances. The optimal duration balances surface quality with dimensional precision.
Technical Deep Dive: Why 5-Axis CNC Unlocks Superior Design
Technical Fact/Rule: 5-axis CNC machines provide unmatched design freedom by moving simultaneously along five different axes.
Functional Implication: This capability creates complex geometries impossible with 3-axis systems, including undercuts, compound curves, and intricate details. The additional axes allow cutting tools to approach a workpiece from multiple angles in a single setup, eliminating manual repositioning.
Strategic/Financial Outcome: Key Metric: 5-axis machining reduces setup time by 60% and improves dimensional accuracy by 40% compared to 3-axis alternatives. This technology enables designs that justify a premium price point, enhancing brand perception and margins.
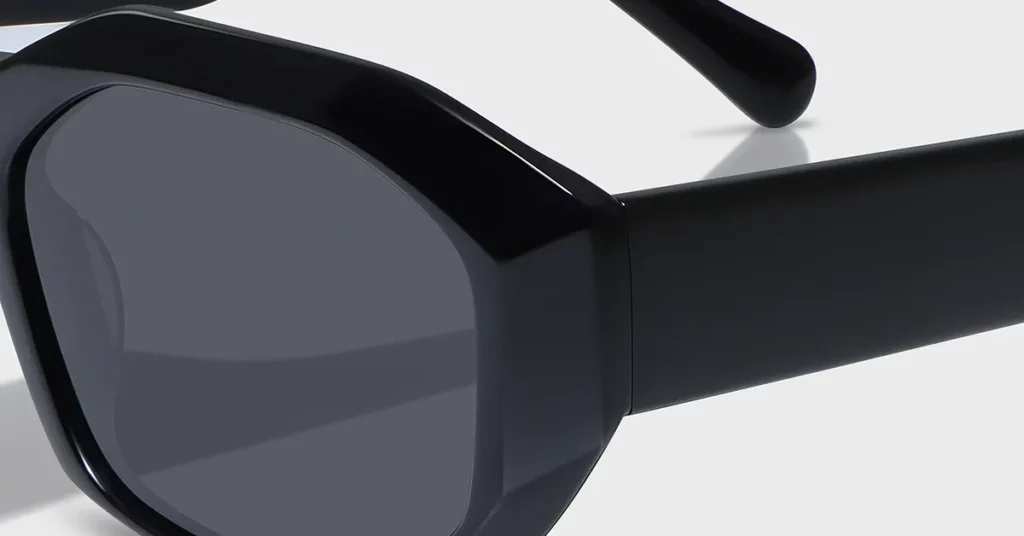
Defining the CNC Quality Standard
CNC machining establishes quality benchmarks that differentiate premium frames.
- Unmatched Precision: The process enables sharp, clean edges and intricate details that cannot be achieved with injection molding.
Key Metric: CNC-machined frames achieve an edge sharpness within a 0.1mm radius, compared to a 0.5mm minimum for injection-molded frames.
- Maximized Material Beauty: Milling reveals the deep, rich color layers of laminated acetate.
For Example: In tortoiseshell patterns, the cutting process reveals different color layers at various sections, creating a three-dimensional depth that enhances authenticity.
- Superior Tactile Experience: The solid-block construction delivers a substantial feel without excessive weight.
The Bottom Line: CNC-machined frames consistently score 15-20% higher in consumer comfort ratings compared to injection-molded alternatives, directly impacting customer satisfaction.
The Business Case for CNC Machining
CNC economics favor market segments where quality and exclusivity outweigh per-unit cost.
Cost Element | Per Frame Cost | Percentage of Total |
Raw Material | $8 – $15 | 25-35% |
Machining Labor | $20 – $35 | 45-55% |
Finishing Operations | $8 – $15 | 15-25% |
Total Manufacturing Cost | $36 – $65 | 100% |
Pro Tips: Leverage CNC flexibility for seasonal collections, limited editions, and designer collaborations that generate premium pricing through an exclusivity narrative. Its low minimum order quantities (MOQs) and rapid prototyping capabilities are ideal for market testing and new product introductions with minimal financial risk.
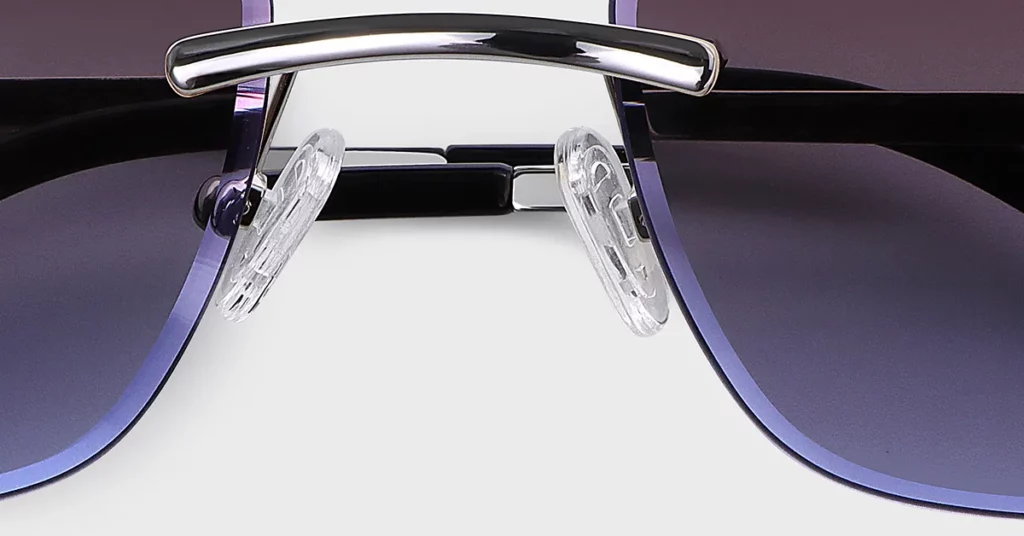
The Injection Molding Playbook: Scalability and Accessibility
Injection molding transforms acetate eyewear manufacturing into an industrial science, enabling consistent quality production at volumes and costs that CNC cannot match.
The Additive Process: From Pellet to Precision
This process relies on controlled material flow into a precision mold, demanding a deep understanding of material behavior, mold design, and process control.
- The Material: The process uses pelletized acetate, which requires careful preparation. Acetate pellets must undergo thorough drying at 70°C for 3-4 hours to eliminate moisture, which causes surface defects and reduces part strength.
- The Tooling: Success depends entirely on mold quality. Premium eyewear molds use hardened steel with surface finishes from mirror polish to specialized textures.
Financial Breakdown: Professional eyewear molds range from $10,000 to over $80,000 for complex, multi-cavity systems.
- The Workflow: The cycle combines high-pressure injection (70-100 MPa), controlled cooling, and automated part removal.
Key Metric: Efficient operations achieve cycle times of 30-60 seconds, enabling production of over 1,000 parts per day from a single-cavity mold.
Critical Warning: Acetate materials degrade rapidly above 240°C. Precise temperature control is mandatory to prevent material degradation and ensure optimal flow.
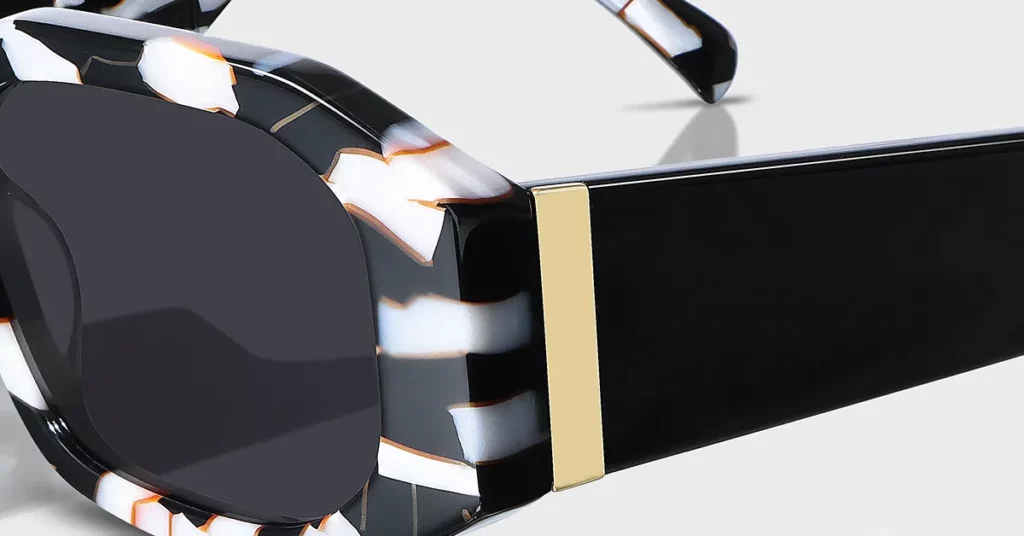
Defining the Injection Molding Quality Standard
Injection molding quality focuses on consistency and repeatability, but it comes with specific design constraints and potential artifacts.
- Design Constraints: You must accommodate draft angles (0.5-2 degrees) for part ejection, maintain uniform wall thickness (1.5-3.0mm), and incorporate a minimum radius of 0.3-0.5mm to eliminate sharp corners.
- Common Defects: Be prepared to manage parting lines, sink marks, ejector pin marks, and flash. Best Practice: Design parting lines in inconspicuous locations to minimize finishing requirements while maintaining aesthetic quality.
- Color and Finish: The process excels at producing consistent solid colors.
Key Metric: Injection molding achieves color consistency within ΔE values of 1.0, ensuring virtually imperceptible variation. However, it cannot replicate the complex laminated patterns of block acetate.
The Business Case for Injection Molding
The economics of injection molding favor high-volume production where tooling investments can be amortized.
Production Volume | Per-Unit Cost | Tooling Amortization | Total Unit Cost |
1,000 units | $3 – $5 | $15 – $50 | $18 – $55 |
5,000 units | $3 – $5 | $3 – $10 | $6 – $15 |
25,000 units | $3 – $5 | $0.60 – $2 | $3.60 – $7 |
The Bottom Line: Injection molding becomes economically attractive at production volumes exceeding 1,000-1,500 units, with optimal efficiency achieved above 5,000 units per design. It is the definitive choice for high-volume orders, price-sensitive segments, and global distribution.
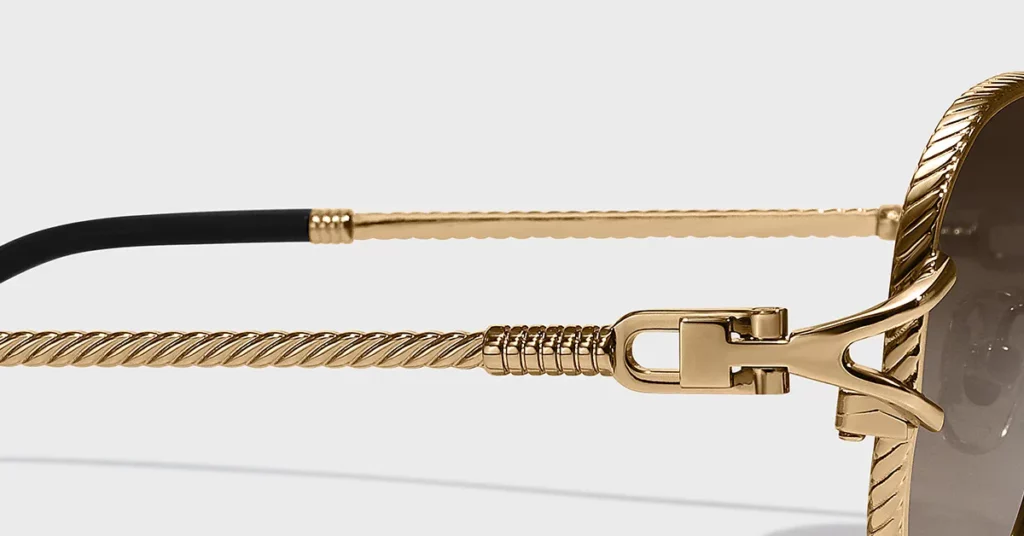
The Strategic Decision Matrix: A Head-to-Head Comparison
Making an informed decision requires a systematic comparison across multiple dimensions that impact your business.
Comparing Product & Quality Outcomes
Attribute | CNC Machining | Injection Molding |
Design Freedom | Unlimited geometric freedom, sharp edges, intricate details. | High-volume repeatability with design constraints (draft angles, radii). |
Aesthetic & Finish | Rich, unique patterns from laminated acetate; deep, hand-polished gloss. | Uniform solid colors; consistent finish controlled by the mold surface. |
Structural Integrity | Maximum durability from solid block construction; no weak points. | Potential for knit lines and internal stresses where material flows meet. |
Final Tactile Feel | Substantial, solid feel with a hand-finished surface. | Lightweight and consistent feel across all units. |
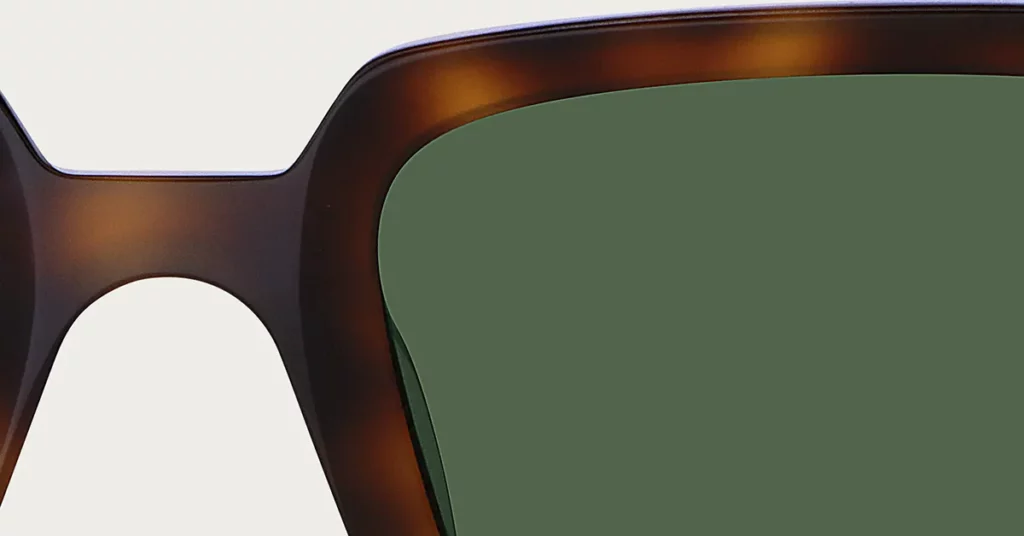
Comparing Business & Operational Factors
Factor | CNC Machining | Injection Molding |
Financial Model | Low capital expenditure (capex), high variable per-unit cost. | High capex (tooling), low variable per-unit cost at volume. |
Scalability & MOQs | Ideal for small batches (MOQ as low as 1); scales linearly. | Engineered for mass production (MOQ 1,000+); scales exponentially. |
Speed & Flexibility | Agile prototyping and rapid design changes (hours/days). | Unmatched per-unit speed in production (seconds), but inflexible design. |
Sustainability | Higher material waste (40-70%), but waste is often compostable. | Higher material efficiency (85-95%), but higher energy use per unit. |
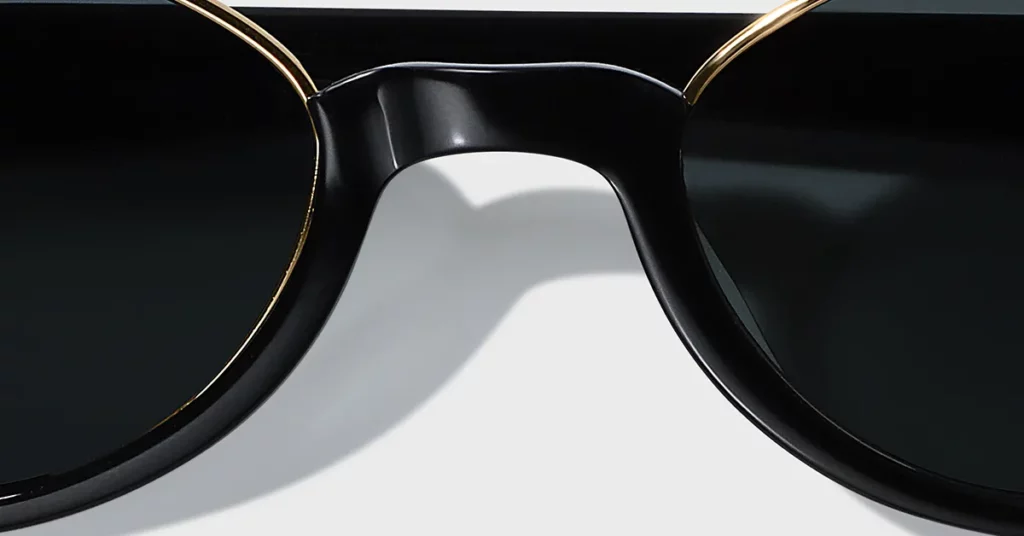
The Partner Vetting Framework: Auditing True Capabilities
Selecting the right manufacturing partner requires a systematic audit of their technical expertise, quality systems, and strategic alignment.
How to Audit a Partner’s CNC Machining Expertise
You must verify a supplier’s claimed capabilities.
- Verify Equipment: Assess the presence and application of 3-axis vs. 5-axis machinery. Demand to see complex parts produced on their 5-axis machines to confirm true simultaneous machining capability.
- Scrutinize Finishing: Evaluate their tumbling methods, polishing compounds, and manual QC standards. Premium finishing requires specialized wooden media and 72-120 hour cycles.
- Demand Material Transparency: Inquire about their acetate suppliers (e.g., Mazzucchelli, Jimei, LA/ES). You must request material certificates of origin and batch documentation to verify sourcing claims.
- Request Proof of Competency: Ask for physical samples of geometrically complex past work. Always conduct your own dimensional verification using precision measurement equipment.
How to Audit a Partner’s Injection Molding Expertise
Evaluation criteria here focus on process control and tooling quality.
- Assess Tooling Capability: Determine if they have in-house vs. outsourced mold design and fabrication. In-house capabilities provide superior control over quality, timing, and modifications.
- Review Process Control: Examine their protocols for mitigating common molding defects. Demand to see process capability studies (Cpk values), which should exceed 1.33 for stable production.
- Confirm Material Handling: Verify they have a standardized process for drying and storing acetate pellets. Proper drying at 70°C for 3-4 hours to below 0.1% moisture is non-negotiable.
- Analyze Production Samples: Request samples from multiple production runs to analyze color consistency (ΔE < 1.0) and finish quality.
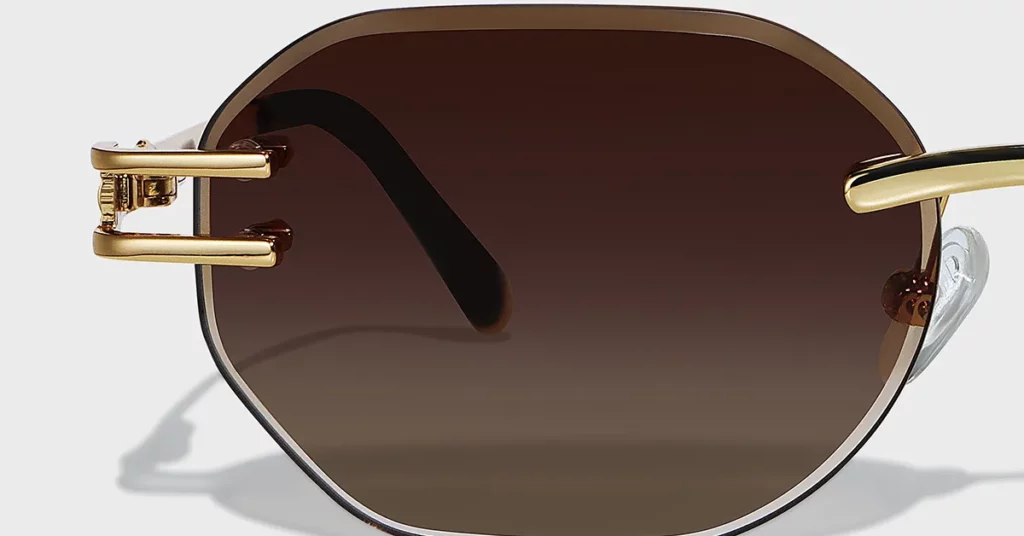
Conclusion
The choice between CNC and injection molding is a strategic decision that defines your brand’s market position. CNC machining delivers the quality and exclusivity for luxury collections, while injection molding provides the scalability for mass-market penetration. Success requires aligning your manufacturing method with your brand objectives.
At Kssmi, our dual expertise in both processes allows us to guide you to the optimal decision for your portfolio.
Frequently Asked Questions
1. How does raw material choice impact final quality?
Mazzucchelli acetate sheets used in CNC machining preserve laminated color structures, creating visual depth impossible with pelletized materials used in injection molding. For molding, premium pellets provide superior processing consistency, but cannot replicate the 3D patterns of block acetate.
2. Can you use a hybrid CNC and injection molding approach?
Yes, creating a CNC frame front with injection-molded temples is feasible. This can optimize cost while maintaining a premium look. However, it adds complexity to supply chain management and quality control for component assembly.
3. What is the real impact of 5-axis vs. 3-axis CNC?
5-axis CNC enables complex geometries like undercuts and compound curves impossible with 3-axis systems. This superior design capability reduces setup time, improves accuracy, and justifies a 40-60% retail price premium, directly supporting luxury brand positioning.
4. What are the costs and lead times for an injection mold?
Multi-cavity steel molds for acetate cost $15,000-$80,000 with lead times of 8-16 weeks. This high upfront investment means the break-even volume is typically 1,500-5,000 units, making it risky for unproven designs.
5. Are there durability differences between CNC and molded frames?
Yes. CNC-machined frames from a solid block are more durable, exhibiting superior resistance to stress and fatigue. They eliminate the potential for weak points like knit lines that can form in injection-molded parts, often resulting in a 15-25% longer service life.