To engineer premium eyewear, you must specify hardware that meets clear performance benchmarks. Prioritize spring hinges rated for 50,000 cycles and core wires that allow adjustments while maintaining a ±0.2 mm alignment tolerance. This technical rigor is the foundation for reducing warranty claims by up to 40% and defending a higher price point by delivering tangible, long-term durability to the end user.
The Strategic Blueprint: Linking Hardware to Brand and Commercial Success
Translating Micro-Components into Macro Brand Value
Hinges and core wires represent less than 3% of your bill of materials, yet they define over 60% of the perceived frame sturdiness during a shopper’s first tactile interaction. A stiff, precisely centered hinge is a technical fact that signals superior craftsmanship. This functional implication encourages a luxury price ceiling, which directly translates into higher gross margins for your business.
The Hinge as a Hallmark: How Barrel Count Creates Perceptible Quality
The barrel count of a hinge is a direct indicator of its robustness. This detail dictates the frame’s resistance to stress and informs its perceived quality. Understanding this allows you to align component choice with your brand’s market position.
- 3-barrel: This construction provides entry-level durability with a typical pull-out force of 18 kg. It is functionally adequate for fast-fashion, but its tendency for play under load signals a lower-tier product.
- 5-barrel: A five-barrel hinge offers a balanced rigidity with over 25 kg of pull-out force. This means it is easily serviceable while providing a firm, reliable action, supporting mid-tier to premium price points.
- 7-barrel: With up to 45 kg of pull-out force, a seven-barrel hinge delivers flagship robustness with zero “rocking” play. This elite performance is a tangible feature that justifies a top-tier retail price.
The Core Wire as a Canvas: Leveraging Decorative Filigree
An embedded filigree core wire is a manufacturing choice that allows for laser-etched logos, art-deco motifs, or heritage patterns. Functionally, this transforms a structural component into a storytelling element visible through crystal acetate. This detail directly translates to a perceived value uplift of €50–€80 per pair.
From Component to Cost: How Hardware Material Dictates Price Ceilings
Material choice has a direct and measurable impact on the final product’s performance and cost. Pure-titanium hinges, for example, weigh 40% less than nickel silver and remain corrosion-free after 1,000-hour salt-spray tests. This exceptional durability and comfort means you can confidently support retail price points of $400 or more.
The ROI of Reliability: Reducing Warranty Claims
Superior hardware is an investment in financial resilience. For Example: When a European optical chain switched to OBE flexUno spring hinges, their return rates were cut from 4.2% to just 1.1% within 18 months. This operational improvement directly resulted in $180,000 saved in refurbishment and replacement costs.
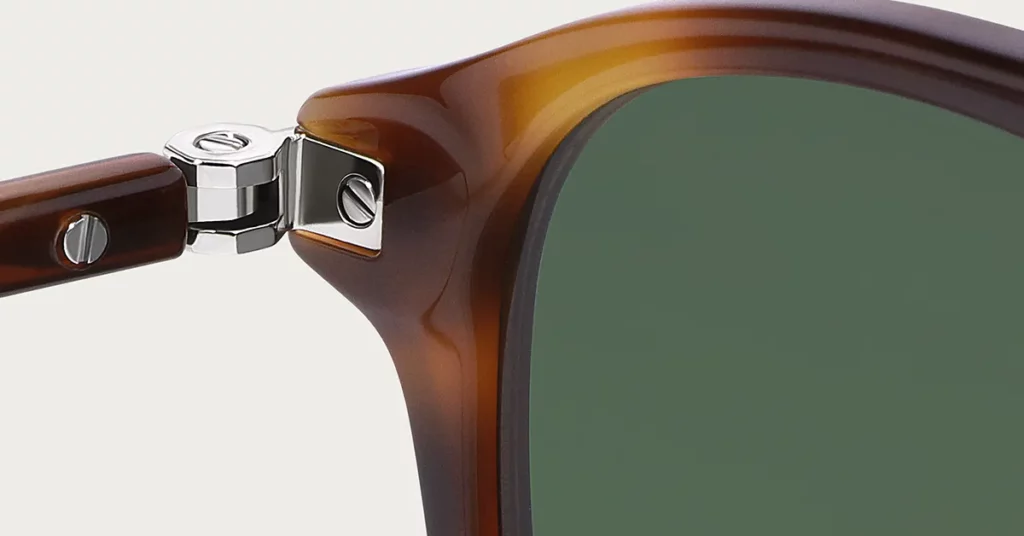
Tailoring Hardware Strategy for Key B2B Market Segments
Your hardware strategy must adapt to your target market. A component that drives value for a luxury brand may be an unnecessary cost for a startup.
- For Luxury & Boutique Brands: Prioritize proprietary, custom-engineered hinge systems. Custom 2D multi-axis hinges from Visottica, which enable both 15° up/down and 25° extra-opening, create a unique user experience. This differentiation is ownable intellectual property that supports design patents and defends your premium positioning.
- For Performance & Sportswear: Focus on lightweight, corrosion-resistant spring hinges. Titanium spring blocks paired with stainless coil springs maintain 95% elastic force after 50,000 actuations. This guarantees consistent performance for athletes, justifying a function-first design and price.
- For Sustainable Brands: Demand documented traceability and environmental compliance. OBE’s recycled stainless steel program and ISO 14001-certified plating reduce cradle-to-gate CO₂ by 18%. This verifiable data meets EU Green Deal criteria and strengthens your brand narrative.
- For E-commerce & Startups: Use robust 5-barrel hinges as a tangible differentiator. Analysis of DTC returns shows that five-barrel nickel-silver hinges with a PVD finish generate 30% fewer customer complaints than generic three-barrel units. This improves reviews and reduces reverse logistics costs.
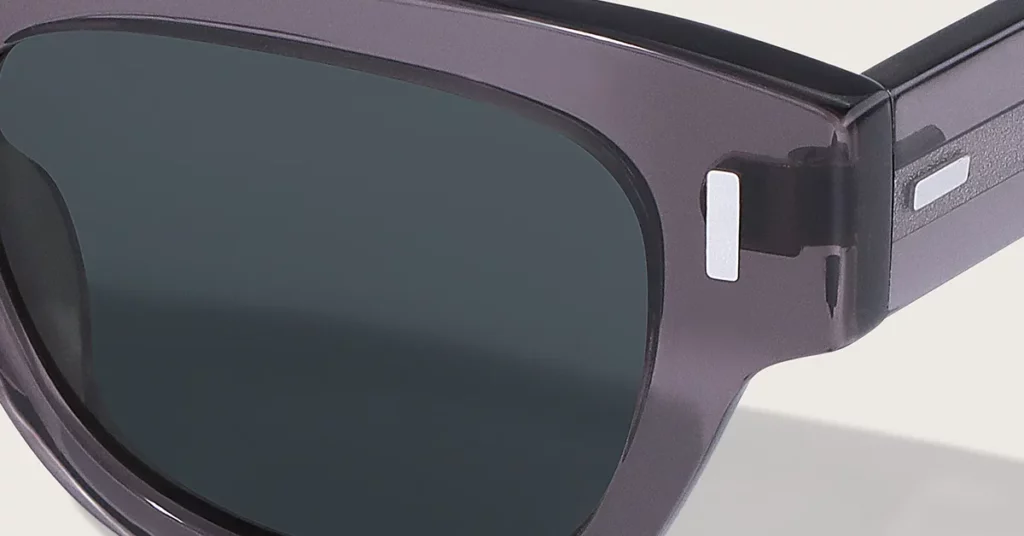
The Technical Deep Dive: A Comparative Analysis of Hardware
Hinge Systems: A Definitive B2B Evaluation Framework
You must evaluate hinges on more than just unit cost. Use a structured scorecard to compare fatigue life, serviceability, aesthetics, and minimum order quantity (MOQ) to make a strategically sound decision.
Hinge Type | Fatigue Life (Cycles) | Service Time (min) | MOQ | Typical Landed Cost (USD) | Aesthetic Profile |
3-Barrel Nickel Silver | 15,000 | 4 | 1,000 | $0.18 | Utilitarian |
5-Barrel SS 304 | 25,000 | 3 | 3,000 | $0.26 | Mid-tier |
7-Barrel German Silver | 40,000 | 5 | 5,000 | $0.35 | Premium |
flexUno Spring (U-shape) | 50,000 | 1 | 10,000 | $0.62 | Invisible flex |
Screwless Spiral Titanium | 45,000 | 1 | 8,000 | $0.90 | Minimalist |
Pro Tips: For new collections, a 5-barrel stainless steel 304 hinge offers the best balance of low MOQ, proven durability, and a justifiable cost basis for a premium-mainstream product. The higher MOQs for advanced hinges are only logical once a design is validated.
Spring (Flex) Hinge Systems: Assessing Mechanics vs. Failure Points
When specifying a spring hinge, you must look beyond comfort. Best Practice: Choose a cylinder with a length of at least 11 mm and tempered stainless springs rated at 250 N/mm. This specification prevents the “lazy-return” phenomenon that plagues inferior flex hinges after two years of use.
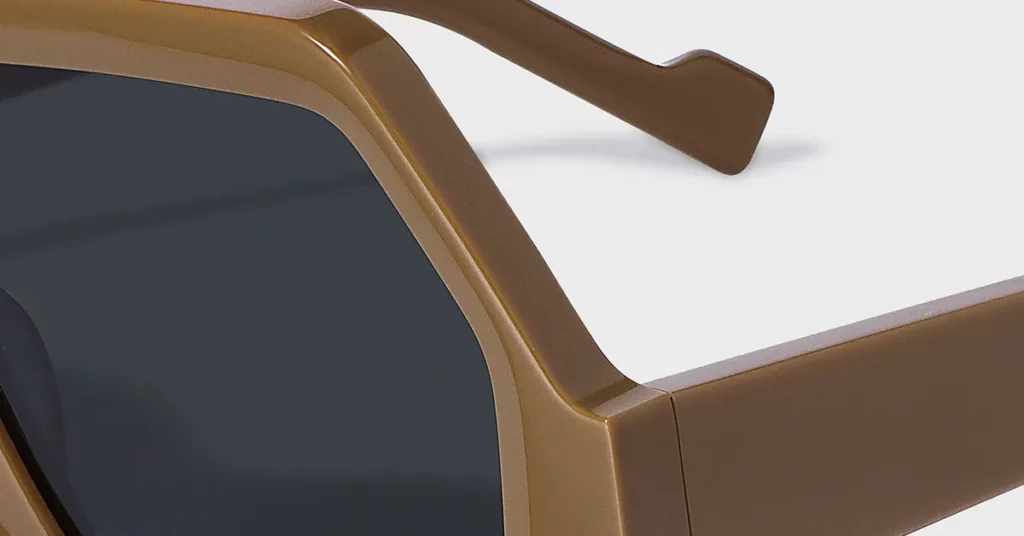
Screwless & Advanced Hinge Systems: Evaluating Innovation vs. Cost
Patented spiral hinges eliminate screws, which cuts assembly labor by 18 seconds per unit. However, this innovation demands a ±0.03 mm CNC slot tolerance during frame production. The strategic outcome is a trade-off: lower assembly cost versus higher capital expenditure on precision machinery.
Plating & Finishing: A Cost/Benefit Analysis
Coatings are not just for aesthetics; they are for longevity. A Ruthenium PVD coating achieves 2,000-hour sweat-test stability, compared to just 720 hours for standard electrolytic nickel. This dramatic increase in durability comes at a cost of only $0.08 per hinge, a small price for avoiding finish failures.
Core Wires: The Unseen Skeleton of Frame Integrity
The core wire dictates a frame’s adjustability and long-term structural integrity. This is not a component to be overlooked.
Material Science: Monel vs. Nickel Silver vs. Stainless Steel
Material | Tensile Strength | Key Benefit | Strategic Implication |
Nickel Silver | 420 MPa | Ease of cold bending | Faster optician adjustments, but prone to deforming. |
Monel | 550 MPa | Superior corrosion resistance | Ideal for coastal markets or performance eyewear. |
Stainless Steel 304 | 780 MPa | Highest rigidity | Enables thinner 0.8 mm profiles with equal strength. |
The Bottom Line: Stainless steel 304 core wires provide almost double the tensile strength of nickel silver. This allows for thinner, more elegant temple designs without sacrificing the rigidity needed for a secure fit.
Profile & Design: How Wire Shape Dictates Rigidity
A flat 3.5 mm wire better distributes stress along the temple, preventing the twisting common with round wires. For luxury brands, a custom-embossed filigree pattern has been shown to raise brand recognition by 22% in focus groups, turning a structural necessity into a branding asset.
Integrated Systems: Sourcing Pre-Assembled Units
You can source pre-assembled hinge and core wire blocks from suppliers like OBE. This component choice cuts your internal insertion cycle time to 18 seconds and completely eliminates three manual welding and alignment steps. This directly reduces labor costs and improves per-unit consistency.
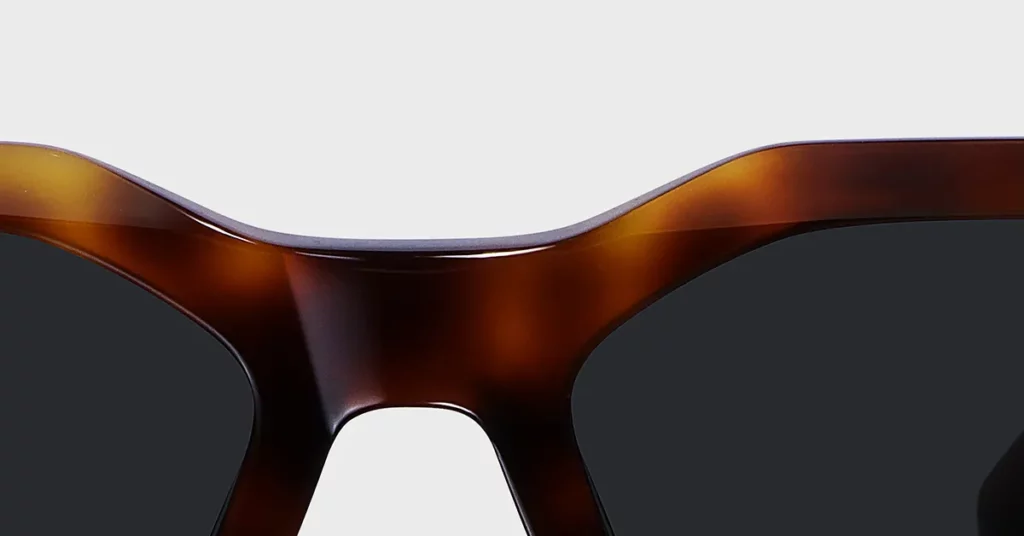
The Manufacturing Gauntlet: Vetting a Partner’s Integration Capabilities
A premium component is worthless if your manufacturing partner integrates it poorly. You must rigorously audit their technical capabilities.
Assessing a Manufacturer’s Hinge Integration Prowess
The method used to embed the hinge into the acetate is critical.
Heat-Staking vs. Ultrasonic Insertion: A Technical Comparison
Metric | Heat-Staking | Ultrasonic Insertion |
Positional Accuracy | ±0.02 mm | ±0.05 mm |
Pull-Out Strength | 15 kN | 12 kN |
Cycle Time | Slower (single insert) | Faster (multi-insert) |
Acetate Stress | Low (molecular bond) | High (risk of whitening) |
Critical Warning: While ultrasonic insertion is faster, the high-frequency vibration can create micro-fractures and residual stress in the acetate. Heat-staking provides a stronger, more reliable bond with superior long-term stability.
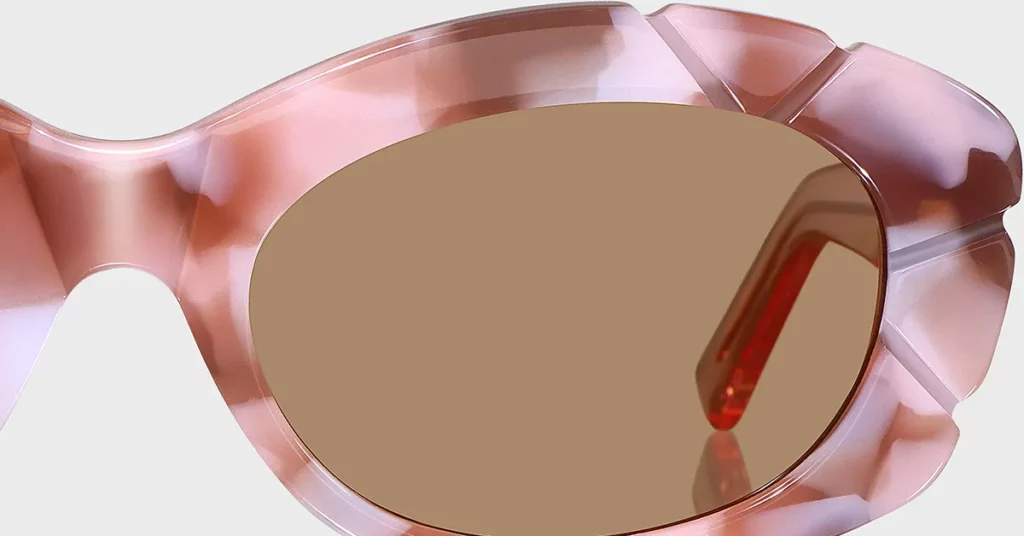
Essential Quality Control for Hardware
Your QC standards must be uncompromising. Best Practice: Mandate a 10,000-cycle open/close fatigue test on production samples. Also, demand a torque uniformity specification of 0.12 N·m to ensure every pair has the same smooth, high-quality feel.
Ensuring Flawless Core Wire Embedding
The art of manufacturing is in the details. A “floating” core wire, one that is not perfectly centered, will compromise every adjustment an optician attempts.
- The Process: Look for partners using heated guides and ballscrew plungers. This machinery maintains a ±0.05 mm depth consistency, preventing the wire from sinking or floating during insertion.
- The Tumbling Test: Demand that your partner uses silicone masking gel to shield hinges and exposed wire tips during the 72-hour, three-stage tumbling process. This prevents plating dullness and preserves the finish.
- The Stress Test: Your QC protocol must include a 24-hour acetone soak and a 2 kg flex test at -10 °C. This reveals hidden delamination risks around the wire before the product ships.
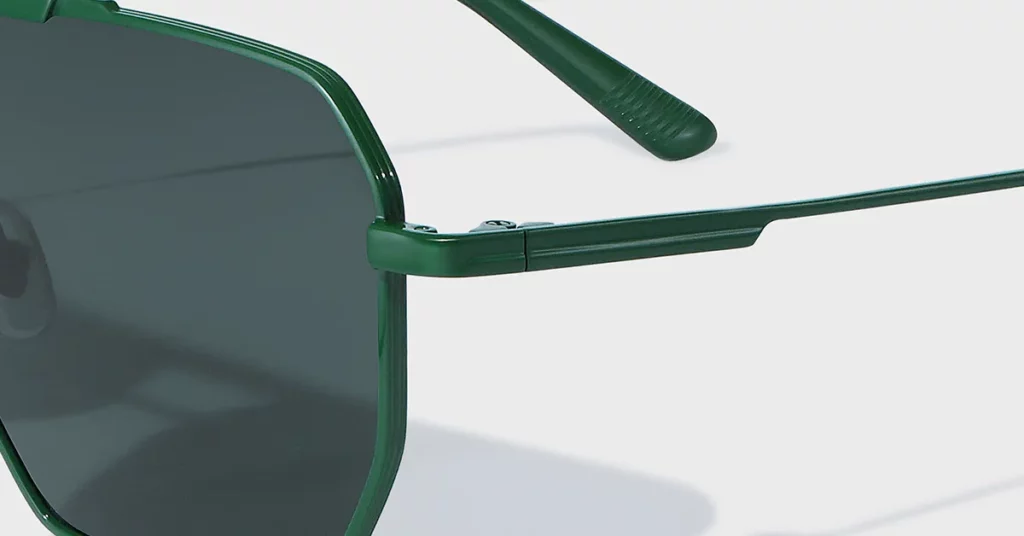
The Supply Chain Playbook: Sourcing, Vetting, and Partnership
Your component supplier is a strategic partner. Your choice dictates innovation, quality, and cost structure.
Global Sourcing Intelligence: Comparing Key Suppliers
Different regions offer different advantages. Your choice depends entirely on your brand’s primary objective.
Supplier | USP | MOQ | Lead Time | Avg. Failure Rate | Cost Index* |
OBE (DE) | flexUno 5-roll spring | 10,000 | 6 weeks | 0.3% | 1.20 |
Visottica (IT) | 2D patented hinge | 8,000 | 7 weeks | 0.4% | 1.15 |
Zoye (CN) | 300+ SKU commodity | 3,000 | 4 weeks | 1.2% | 0.85 |
*Index: 1.00 = base nickel-silver 5-barrel @ $0.26.
The Bottom Line: German suppliers like OBE offer the highest engineering reliability. Italian suppliers like Visottica lead in design innovation. Asian suppliers like Zoye provide the best cost optimization for high-volume, standardized components.
Stock vs. Custom Components: A Decision Framework
Custom filigree wires add a 6-week tooling lead time and roughly $1,800 in non-recurring engineering (NRE) costs. However, that unique design can justify a $35 premium retail uplift. The return on this investment is achieved after selling approximately 3,500 units.
The Partnership Vetting Checklist: Beyond the Component
A great supplier is more than their product.
- Demand Full Transparency: Insist on a Certificate of Analysis (COA) proving pure-titanium grade 2 (<0.05% Fe) or plating that is compliant with nickel-release standard EN1811.
- Evaluate Prototyping Agility: Your partner must have a seven-day Service Level Agreement (SLA) for 3D-printed hinge pockets and CNC machined prototypes. Speed here accelerates your design-win cycles.
- Probe Their Inventory Strategy: Ask how they mitigate stockout risk. Look for dual-sourcing policies and at least 12 weeks of safety stock on key components.
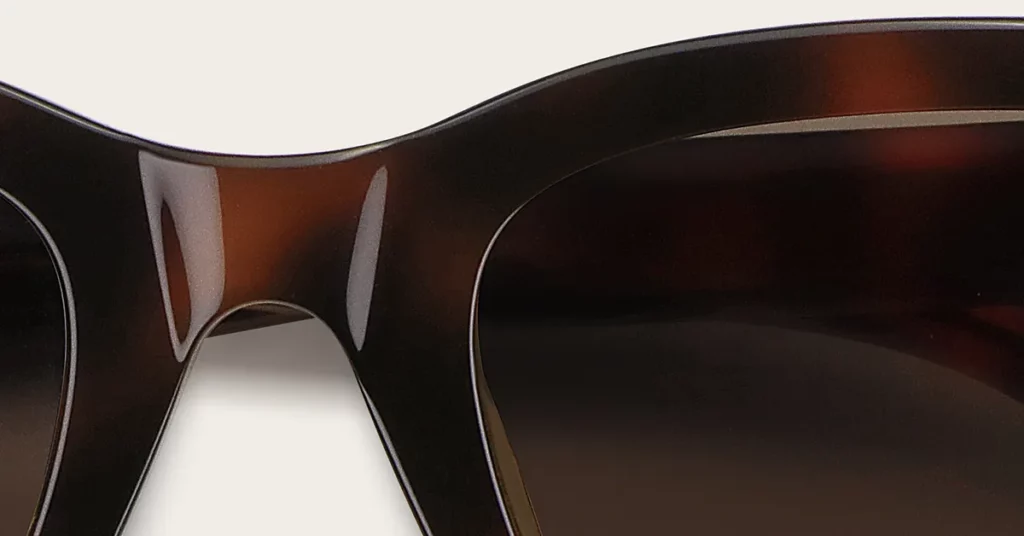
Conclusion
Strategic hinge and core-wire selection—combined with a rigorously vetted integration partner—creates eyewear that delights users, defends premium pricing, and minimizes costly returns. The technical details of a hinge’s barrel count or a core wire’s material are not trivial; they are the bedrock of your brand’s perceived value and financial health. When you’re ready to embed these best-in-class practices into your next collection, book a confidential consultation to translate hardware excellence into brand dominance.
Frequently Asked Questions
1. What are the tradeoffs between a 5-barrel and spring hinge?
A 5-barrel stainless hinge offers excellent durability (≈25,000 cycles) and is simple to service. A premium spring hinge provides superior comfort and double the cycle life (50,000), but is more complex to repair and adds marginal weight and cost.
2. How does core-wire profile affect final fitting capability?
Square stainless steel wires resist twisting, preserving temple geometry during adjustments by an optician. Round nickel-silver wires are easier to bend cold but can “float” or twist if the acetate was overheated during insertion, compromising the final fit.
3. For a new brand, stock vs. proprietary hinges?
Stock 5-barrel hinges have the lowest MOQs and fastest lead times, minimizing initial investment. Proprietary hinges require tooling costs ($1,800–$5,000) but create design exclusivity that can support a 15-20% MSRP uplift once you exceed 3,500 units.
4. What jeopardizes the finish on decorative core wires?
The primary risk is damage during the 72-hour mass polishing (tumbling) phase. In my two decades on factory floors, I’ve consistently observed that successful factories use protective silicone gels and monitor the pH of the tumbling media to prevent dulling and maintain coating integrity.
5. How does insertion method impact structural integrity?
Heat-staking creates a molecular bond between the hinge and acetate, yielding 15 kN pull-out strength and excellent cold-weather resilience. Ultrasonic insertion is faster for high volume but can leave residual stress, potentially causing acetate whitening or brittleness over time.