Acetate eyewear manufacturing is a multi-stage process where raw cellulose acetate blocks are cured for 8-12 weeks, precision-cut using 5-axis CNC machines, and polished for 72-100+ hours in tumbling barrels. The final frames are hand-finished to achieve a signature luster. This meticulous process ensures material stability, durability, and the premium aesthetic that justifies a higher retail price point, directly impacting your brand’s market position and profitability.
Critical Warning: The acetate manufacturing process demands 8-12 weeks of curing time before cutting can begin. Any manufacturer offering shorter timelines is actively compromising material stability, which exposes your brand to long-term reputational damage from product failure.
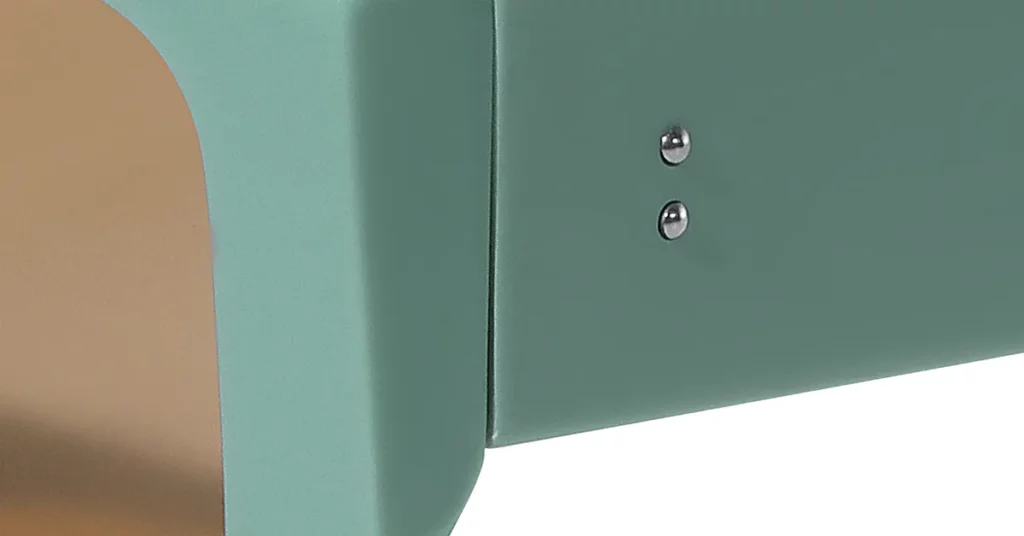
The Raw Material: From Natural Origins to Cured Block
The foundational stage of production determines an acetate frame’s stability, color depth, and long-term durability. These factors directly influence your product’s market performance and customer satisfaction. Every decision here is a financial one, impacting your final cost of goods and potential retail margin.
The Purity of the Source
Premium acetate manufacturing starts with cotton linters and wood pulp with cellulose purities of 90% or higher. This high cellulose content is a technical requirement because it provides the structural integrity and workability essential for precision eyewear production. This translates to fewer defects during machining, which protects your production timelines and unit costs.
The Role of Plasticizers
Plasticizers determine acetate’s flexibility and long-term performance. Traditional formulations use DEP (diethyl phthalate) plasticizers, while premium manufacturers now offer bio-based alternatives. For brands targeting eco-conscious consumers, Mazzucchelli’s M49 formulation replaces phthalates with plant-based solutions. This meets sustainability mandates without compromising performance, which directly supports a higher price point.
For Example: Bio-based plasticizers eliminate plasticizer migration, a chemical reaction that causes clouding in polycarbonate lenses. This technical compatibility removes a significant product failure risk, protecting your brand from warranty claims and preserving customer trust.
The Curing & Seasoning Process
Proper curing is the most critical quality control checkpoint in acetate production. Freshly cast acetate blocks must undergo conditioning for a minimum of 8-12 weeks at 20-25°C and 45-55% relative humidity. This extended process removes residual solvents and relieves internal stresses. This is the only way to guarantee dimensional stability, which prevents the warping and cracking that leads to costly product returns.
Key Metric: Properly cured acetate exhibits a moisture content of approximately 2% at 50% relative humidity. This provides the ideal balance between workability for manufacturing and stability for the end user. Demand this specification from your supplier.
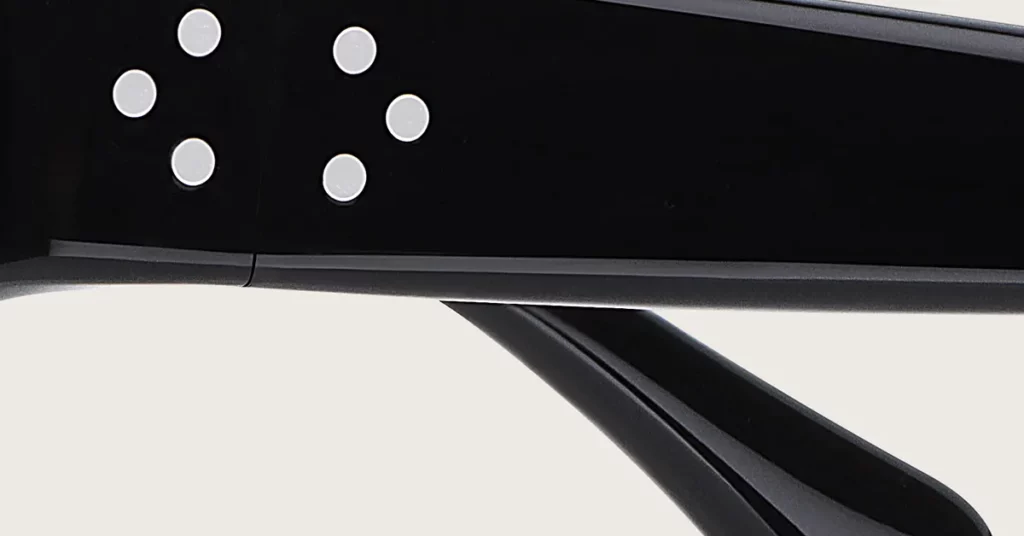
Strategic Material Sourcing: A Framework for Quality
Your material selection directly impacts manufacturing efficiency, final product quality, and market positioning. Understanding the technical differences between acetate types enables informed sourcing decisions that optimize both production costs and finished product performance.
Block Acetate vs. Extruded Acetate
Feature | Block Acetate | Extruded Acetate |
Color Depth | Rich, Complex, Layered | Uniform, Limited Patterns |
Structural Integrity | Superior | Good |
Pattern Complexity | Unlimited (e.g., “Havana”) | Limited |
Production Time | 6-8 weeks | 2-3 weeks |
Material Cost | Premium | Standard |
Best Practice: Specify Italian block acetate for luxury collections where color complexity and brand prestige justify premium pricing. The unique patterns are impossible to replicate with other methods, creating a defensible competitive advantage. Reserve extruded acetate for volume production where cost optimization is the primary driver.
The Rise of Bio-Acetate
Bio-acetate employs renewable, plant-based plasticizers instead of petroleum-based ones. The functional implication is that the material maintains identical performance characteristics, meaning you can meet sustainability demands without compromising product quality or manufacturing processes. This allows your brand to access the growing market of environmentally-conscious consumers.
Translating Material to Market
Material properties directly influence consumer perception and brand value. Acetate’s hypoallergenic properties appeal to consumers with sensitive skin, while its adjustability allows opticians to provide a custom fitting. These are value propositions unavailable with injection-molded alternatives, and they are key drivers of your product’s retail price.
The Bottom Line: Premium acetate material represents 15-25% of your total production cost but enables 40-60% higher retail pricing. This is achieved through superior aesthetics and performance characteristics that consumers can see and feel, creating a strong return on your initial investment.
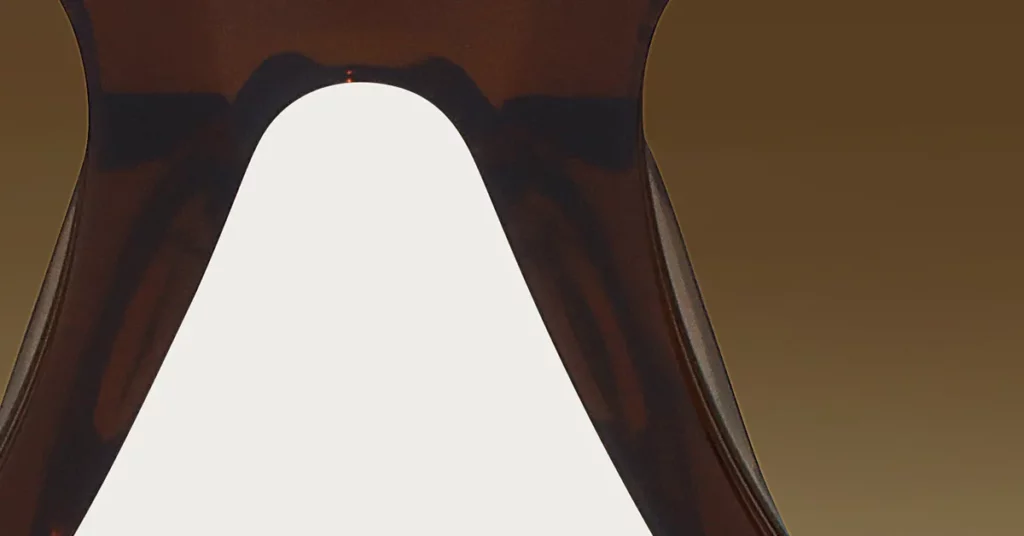
The Manufacturing Journey: From Block to Component
The transformation from acetate block to precision frame components requires sophisticated CNC machining and skilled programming. This stage determines dimensional accuracy and surface finish, factors that directly impact your manufacturing costs and product quality.
Precision CNC Milling
Modern acetate frame production relies on 5-axis CNC milling machines capable of achieving tolerances within ±0.1mm. The functional implication is that these machines can perform complex cuts for lens grooves and hinge pockets in a single program. This reduces handling errors and improves consistency, which directly translates to lower defect rates.
Critical Warning: Incorrect cutting parameters, such as using dull carbide tools or the wrong feed rates (2,000-3,000 mm/min is optimal), cause material stress concentrations. These invisible micro-fractures manifest as cracks weeks after production. Always verify your manufacturer’s CNC programming expertise and tool maintenance logs.
CNC Routing vs. Laser Cutting
Factor | CNC Routing | Laser Cutting |
Edge Quality | Excellent (Polished) | Good (Requires Finishing) |
Material Waste | 15-20% | 10-15% |
Processing Speed | Moderate | Fast |
Heat Impact | None | Significant |
Ideal Use | Production Runs | Rapid Prototyping |
Pro Tips: While laser cutting is faster, the heat-affected zones it creates can cause plasticizer loss and material embrittlement at the cut edges. For final production, demand CNC routing to ensure the material’s structural integrity is never compromised.
Strategic Nesting Software
Advanced nesting software optimizes component layout to maximize the number of frames cut from a single acetate block. This software can increase material utilization rates to 80-85%. The strategic outcome is a direct reduction in your material costs by 20-30% while ensuring color and pattern consistency across a single frame.
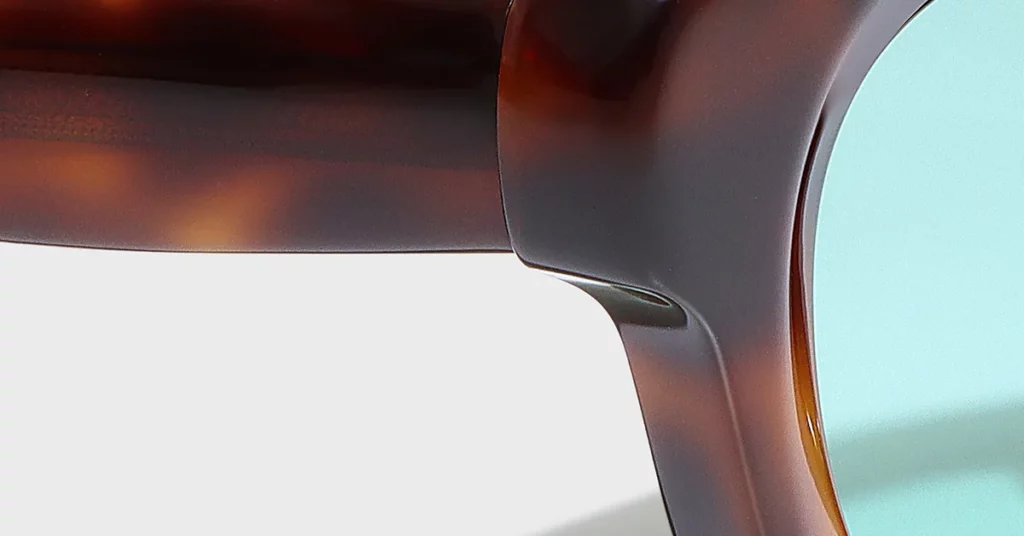
Shaping and Reinforcement: Creating 3D Contours
This process transforms flat acetate components into ergonomic, three-dimensional products. It requires precise temperature control and skilled craftsmanship to achieve consistent results without degrading the material.
The Heat Pressing Process
Heat pressing uses specialized molds to create the frame’s curvature, heating the acetate to 90-100°C. This controlled heating allows the material to take the shape of the mold, forming ergonomic facial curves and bridge bumps. The strategic outcome is a frame that provides superior comfort, a key driver of customer satisfaction and brand loyalty.
Inserting a Metal Core Wire
Temple reinforcement involves inserting a metal core wire into heated acetate temples using a “wire shooting” process. This provides the structural support and adjustability required for a proper optical fitting. This reinforcement prevents temple breakage, which directly reduces warranty claims and protects your brand’s reputation for durability.
Premium Technique: Cold-Insert Core Methods
Cold-insert methods utilize precision-drilled channels to insert the metal core wire without heating the acetate. This technique eliminates all risk of thermal stress and dimensional changes. While it requires superior machining capabilities, the result is a frame with better long-term stability, justifying a premium price for luxury collections.
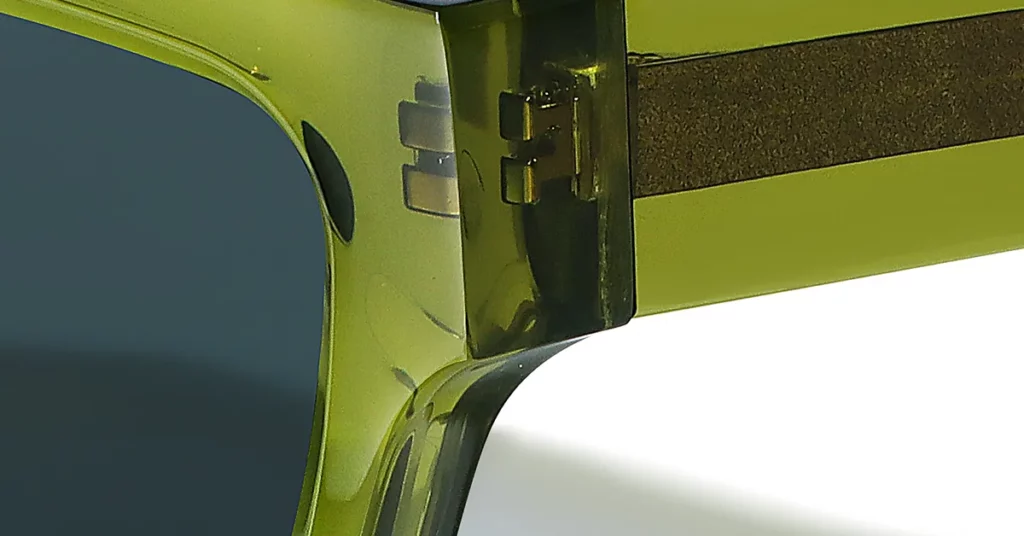
Assembly: Building a Durable, Long-Lasting Frame
Assembly quality determines the final frame’s durability and functionality. The choice of assembly methods and hardware directly impacts product reliability and the perceived value of your eyewear.
Riveting vs. Heat-Staking Hinges
Riveting creates a permanent, high-strength mechanical bond suitable for premium frames. In contrast, heat-staking melts the acetate around the hinge, which is a lower-cost assembly method that can compromise long-term reliability. Prioritize riveting because it produces a more durable and repairable product, reinforcing the quality promise that underpins a premium price.
Hinge Barrel Analysis
Hinge Type | Durability Rating | Cost Factor | Application |
3-Barrel | Good | 1.0x | Standard Frames |
5-Barrel | Excellent | 1.5x | Premium Frames |
7-Barrel | Superior | 2.0x | Luxury Collections |
Pro Tips: Higher barrel counts distribute stress across a larger contact area, which reduces wear and extends the service life of the frame. The visual impact of 5- and 7-barrel hinges also conveys a higher standard of quality to the consumer before they even try the frame on.
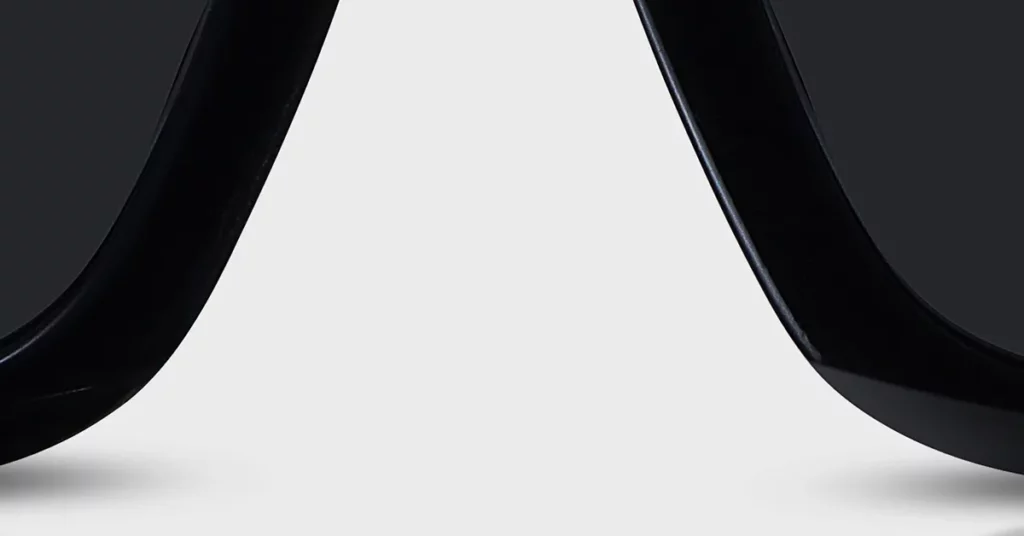
Finishing: The Signature Luster of Luxury Eyewear
The tumbling process is the most time-intensive stage of production, transforming rough-machined components into smooth products ready for final polishing. This stage is non-negotiable for achieving a premium look and feel.
The Science of Barrel Tumbling
Barrel tumbling utilizes octagonal drums filled with hardwood chips (typically birch) and polishing pastes for 72-100+ hours. This multi-stage process gradually refines the surface.
- Stage 1 (12 hours): Dry roughing with pumice to remove machine marks.
- Stage 2 (12 hours): Smoothing with finer pumice to eliminate surface imperfections.
- Stage 3 (18 hours): Polishing with specialized creams to develop initial luster.
- Stage 4 (18 hours): Final buffing to create a mirror-like finish.
Polishing & Hand-Finishing
After tumbling, high-speed polishing wheels operating at 3,000-5,000 RPM with Tripoli and rouge compounds create the final mirror finish. This is followed by hand-beveling, where artisans use specialized tools to create subtle edge refinements. This human touch creates a level of detail and tactile quality that automated processes cannot replicate, providing a clear differentiator for luxury-tier products.
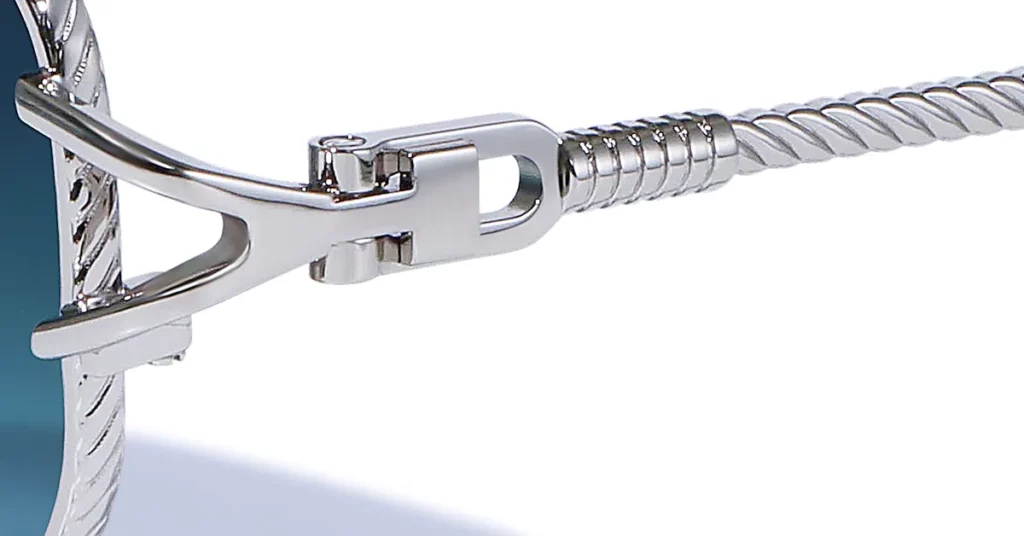
Final Alignment: The Last Checkpoint for Perfection
Final assembly and alignment are where precision components become functional, aesthetically pleasing eyewear. This is the last opportunity to ensure the product meets quality standards before it reaches your customer.
Precision Lens Grooving
The lens groove must be cut to a tolerance of ±0.05mm to ensure secure lens seating. This precision is a technical requirement because it prevents lens movement and distributes stress evenly around the frame. This directly impacts the optical performance and long-term durability of the eyewear.
The Art of “Trueing”
“Trueing” is the manual frame alignment process to ensure perfect symmetry and fit, with tolerances within 0.5mm. This requires skilled technicians who manually adjust temple alignment and bridge symmetry. A properly trued frame guarantees correct optical alignment, preventing the visual distortion and discomfort that lead to customer complaints.
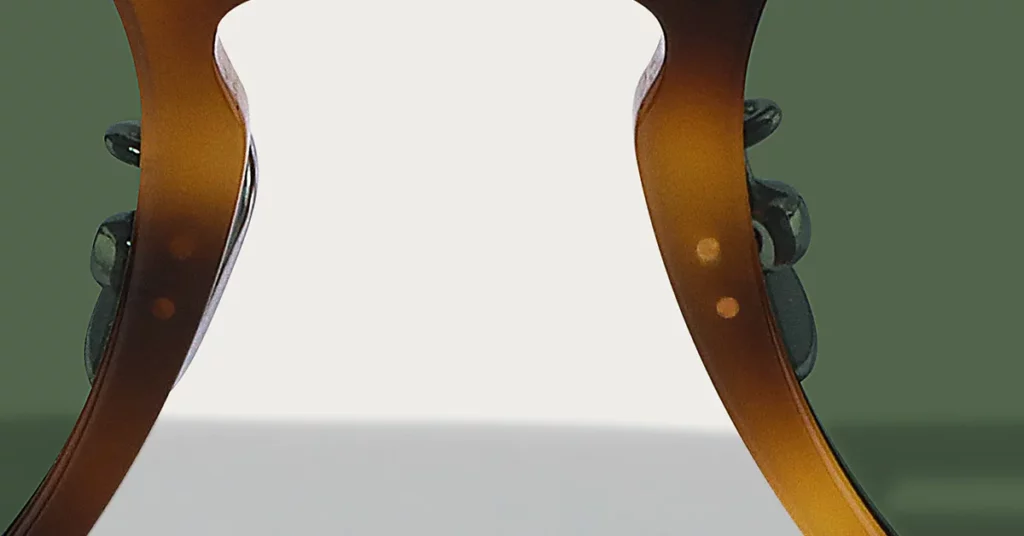
Competitive Analysis: Acetate vs. Alternative Technologies
Understanding the trade-offs between machined acetate and injection-molded plastic enables you to make informed material selections that align with your brand’s specific cost structure and market position.
Machined Acetate vs. Injection-Molded Plastic
Quality Factor | Machined Acetate | Injection-Molded Plastic |
Color Depth | Rich, Complex | Uniform, Limited |
Tactile Feel | Premium | Standard |
Durability | Excellent | Good |
Customization | High (Small Batches) | Low (High MOQs) |
Production Speed | 8-12 frames/hour | 100-200 frames/hour |
Market Position | Premium / Luxury | Mass Market |
The Role of 3D Printing
3D printing, particularly Selective Laser Sintering (SLS), is a powerful tool for rapid prototyping. It allows you to test fit and form in days rather than weeks, compressing your design cycle before committing to costly production tooling. While its material properties and surface finish currently limit its use for mass production, it offers unique potential for creating bespoke geometries in niche, ultra-premium collections.
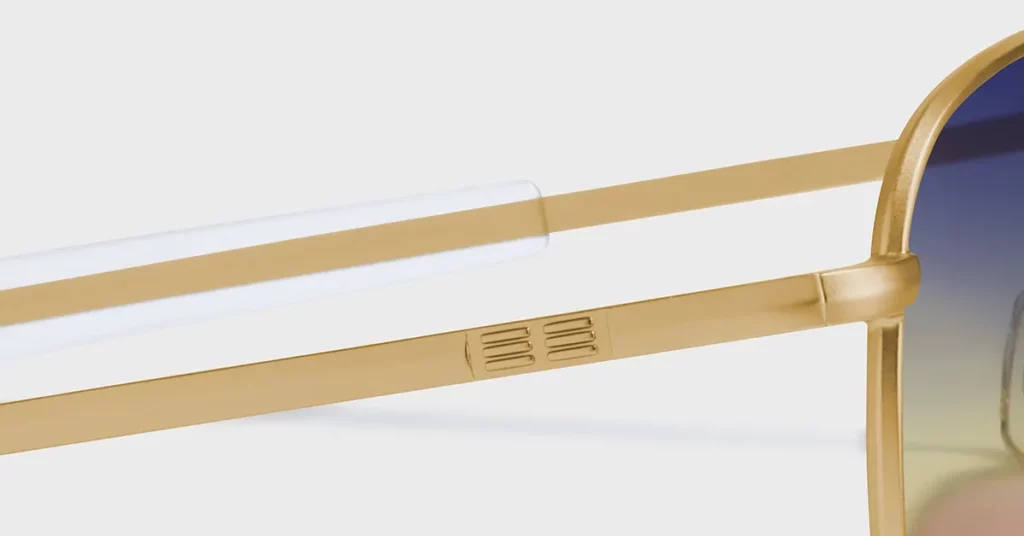
The Vetting Framework: How to Audit a Manufacturer
A comprehensive quality control system protects your brand and ensures consistent product delivery. Use this framework to conduct effective manufacturer evaluations and monitor performance.
Critical Quality Control Checkpoints
- QC Step 1: Inbound Material Verification. Demand verification of acetate thickness (tolerance ±0.05mm), color consistency against approved samples, and a defect inspection for bubbles or inclusions.
- QC Step 2: In-Process Technical Audits. Verify CNC tolerances with precision gauges, check hinge alignment using specialized fixtures, and confirm core wire placement to prevent stress concentrations.
- QC Step 3: Final Product Testing. Require conformance reports for ISO 12870, which governs eyewear quality. This includes tests for dimensional stability, mechanical strength, and finish quality under controlled lighting.
The B2B Audit Checklist
When evaluating a potential partner, demand clear answers to these 10 questions about their acetate process:
- What is your exact acetate curing timeline and what are your environmental controls?
- How do you guarantee color consistency across different production batches?
- What are your in-house CNC programming capabilities for design modifications?
- How many distinct tumbling stages do you use and what is the duration of each?
- What are your specific quality control checkpoints throughout the production line?
- What is your process for handling custom design modifications mid-production?
- What is your production capacity for handling seasonal demand spikes?
- How do you ensure continuous skill training for your hand-finishing artisans?
- What international quality certifications (e.g., ISO) do you currently hold?
- What is your formal process for handling quality failures and what are your warranty provisions?
Cost-Benefit Analysis
Investing in premium manufacturing processes increases production costs by 25-40%. However, this investment enables retail price premiums of 60-100% through superior, verifiable quality. This cost-benefit relationship creates a strong, positive ROI for brands targeting quality-conscious consumers, enhancing brand equity and delivering superior margin.
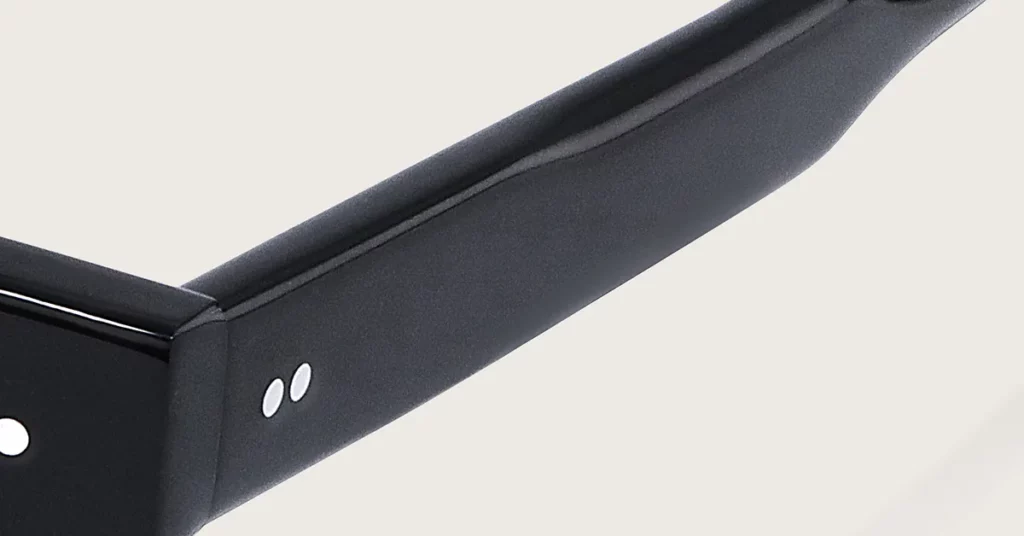
Conclusion
Understanding the complete acetate manufacturing process provides the knowledge to evaluate manufacturer capabilities, ensure quality, and optimize your brand’s position. The complexity of transforming raw acetate into premium eyewear requires a partner who combines advanced equipment with skilled craftsmanship.
This technical mastery is the foundation of a product that can command a premium price and earn lasting customer loyalty. Contact Kssmi to discuss how our acetate manufacturing expertise can elevate your brand.
Frequently Asked Questions
1. What issues arise from rushed acetate curing?
Improper curing leads to dimensional instability, warping, and stress cracking. Rushed curing leaves residual solvents, causing frames to change shape or develop cracks near hinges over time, leading to product failures.
2. What is the difference between 3-axis vs. 5-axis CNC?
5-axis machines create complex geometries and hinge pockets in a single setup, improving accuracy and surface quality. 3-axis machines require multiple setups for complex frames, which increases the risk of error and handling marks.
3. Is hand-polishing necessary after barrel tumbling?
Yes. Barrel tumbling creates a uniform surface but cannot properly finish detailed areas like lens grooves. Hand-polishing provides the precision required for these areas, creating a superior overall finish that differentiates a premium product.
4. How is “Havana” acetate different from solid-color acetate?
“Havana” blocks are made by layering multiple colored sheets before pressing, a complex process that increases material cost by 40-60%. This method requires longer curing and enhanced QC to prevent delamination.
5. What are the risks of using too much heat to insert a core wire?
Excessive heat (above 90°C) causes material bubbling, dimensional distortion, and plasticizer loss, which makes the acetate brittle. Quality manufacturers use precise temperature control and skilled operators to mitigate these risks completely.