Regulatory compliance is not a legal burden; it is your strategic advantage. A bulletproof compliance strategy protects your brand, accelerates market entry, and builds the consumer trust necessary for premium positioning. Critical Warning: Non-compliance leads to product seizures, import bans, and irreversible damage to your brand’s reputation. The investment in proper compliance is an investment in market access and stability.
Entering the U.S. Market: Mastering FDA Regulations
The FDA regulates sunglasses as Class I medical devices, a classification that many fashion brands underestimate. This is because sunglasses serve the medical purpose of protecting the eyes from harmful UV radiation. Understanding this classification is the first step to securing access to the U.S. market.
Why Sunglasses are Class I Medical Devices
The FDA’s classification of sunglasses under 21 CFR 886.5850 is based on their function, not their fashion. This rule means they are subject to general controls, including registration, listing, and specific performance standards. While they are exempt from pre-market notification (510(k)), this exemption is contingent on you making no therapeutic claims beyond basic sun protection.
The Mandatory Drop Ball Protocol (21 CFR 801.410)
The drop ball test is the FDA’s primary gatekeeper for impact resistance. The rule states that lenses must withstand a 0.56-ounce steel ball dropped from a height of 50 inches. This functional requirement means your product’s material and design must be inherently robust, which directly translates into a safer product and a lower risk of liability.
- Glass Lenses: Each prescription lens must be individually tested.
- Non-Prescription Lenses: Statistical sampling from production batches is permitted.
- Plastic Lenses: Batch testing using statistically significant samples is the standard.
- Test Conditions: The steel ball must strike within a 5/8-inch diameter circle at the geometric center of the lens.
A lens fails if it fractures completely or if any material detaches from the surface facing the eye.
Pro Tips: You can use alternative testing methods if they are “equal or superior” to the drop ball test, but you must maintain meticulous records proving their equivalency.
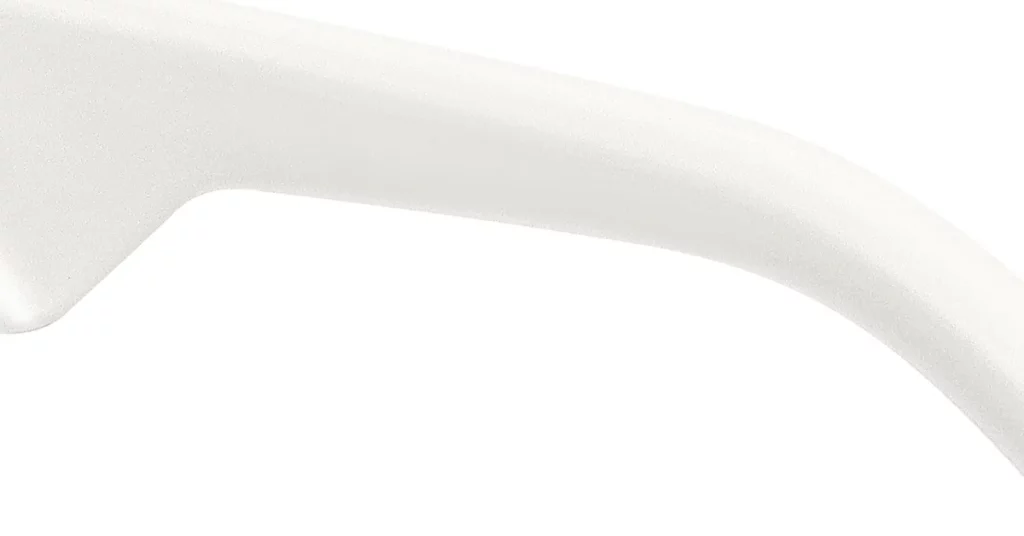
The Administrative Hurdle: FDA Registration
FDA registration is the paper trail that grants you market access. You must complete these steps before your first shipment lands.
- Establishment Registration: You must register your manufacturing facility annually through the FDA’s FURLS system.
- Device Listing: Each sunglass model must be listed with its specific product code, typically HQY (Sunglasses).
- Official Correspondent: You must designate a formal contact for all FDA communications.
- Annual Renewal: Registration must be renewed between October 1st and December 31st each year.
For Example: A Chinese manufacturer must register its facility, list its products under code HQY, and appoint a U.S. Agent to manage FDA communications. Failure to maintain active registration will result in your products being blocked at the port of entry.
The Business Cost of Failure: Import Alerts and Detentions
The FDA’s enforcement tools can liquidate your inventory and blacklist your company. An import alert allows the FDA to detain your products without physical examination based on past non-compliance. This means a single failure can poison your entire supply chain, making prevention far more cost-effective than remediation.
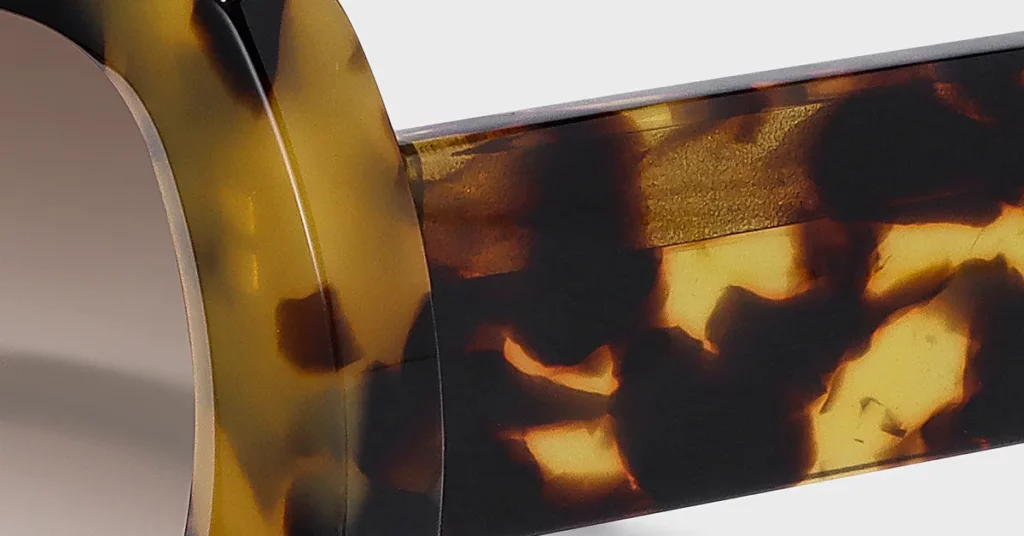
Unlocking the European Union: The CE Mark for PPE
The European Union classifies sunglasses as Category I Personal Protective Equipment (PPE) under Regulation (EU) 2016/425. This regulation treats sunglasses as equipment designed to protect the user from the “minimal risk” of sunlight-induced eye injury. Your strategy for the EU market hinges on mastering this framework.
Understanding PPE Regulation (EU) 2016/425
Category I PPE allows for self-declaration of conformity, which means you do not need a third-party notified body to approve your product. This places the full legal responsibility on you, the manufacturer, to guarantee compliance. This requires a rigorous internal process of risk assessment and documentation before you can affix the CE mark.
Presumption of Conformity via EN ISO 12312-1
Following the harmonized standard EN ISO 12312-1:2022 is the most direct path to EU compliance. Adherence to this standard creates a “presumption of conformity,” which means regulatory authorities will consider your product compliant with the essential health and safety requirements of the PPE Regulation. This standard streamlines your development and testing protocol.
The Technical File and Declaration of Conformity (DoC)
Your technical file is the legal foundation of your CE mark. It is the collected evidence that proves your product is compliant, and you must maintain it for 10 years.
- Product Description: Detailed specifications, materials, and construction diagrams.
- Risk Assessment: A thorough analysis of all potential hazards and the measures taken to mitigate them.
- Test Reports: The complete, unabridged results from testing against EN ISO 12312-1.
- Design Documentation: All drawings, material specifications, and manufacturing procedures.
The Declaration of Conformity (DoC) is your formal, legally binding statement that the product meets all EU requirements. You must be prepared to provide this document to any EU authority upon request.
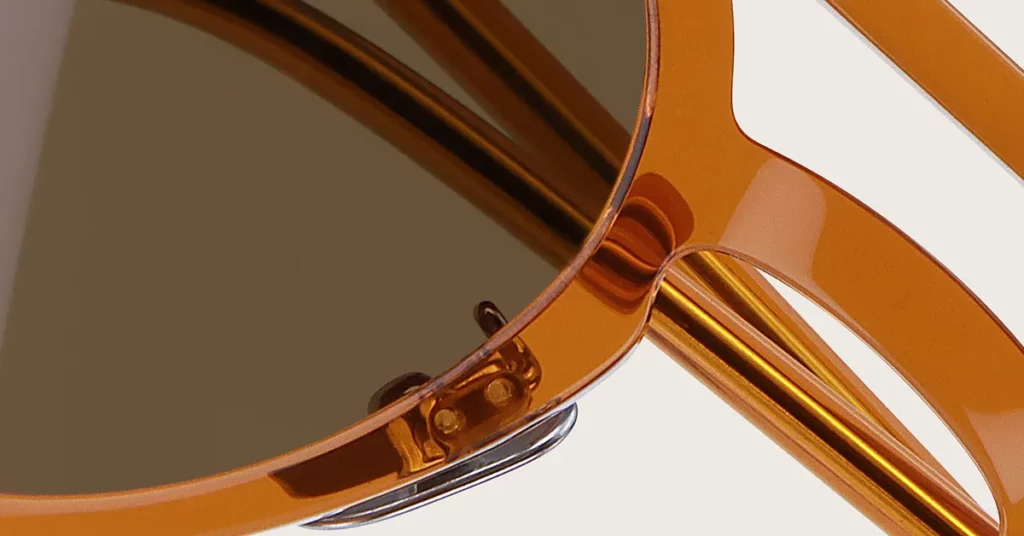
The Global Benchmark: Technical Requirements of ISO 12312-1
ISO 12312-1:2022 is the international technical benchmark for sunglasses. Mastering its requirements allows you to engineer a single product that can be sold in multiple global markets with minimal modification, delivering significant economies of scale.
Performance Metrics for UV Protection
The primary function of sunglasses is UV protection. The ISO standard sets non-negotiable transmittance limits to protect against invisible radiation.
Critical Warning: You cannot assess UV protection visually. Only calibrated spectrophotometric testing can verify that a lens meets these requirements.
- UVA Protection: Transmittance must not exceed a specified value in the 315-380nm range.
- UVB Protection: Very strict transmittance limits are enforced in the 280-315nm range.
- UV400 vs. Standard: The standard requires protection up to 380nm. A “UV400” claim means you are providing protection up to 400nm, which exceeds the standard and can be a valuable marketing claim.
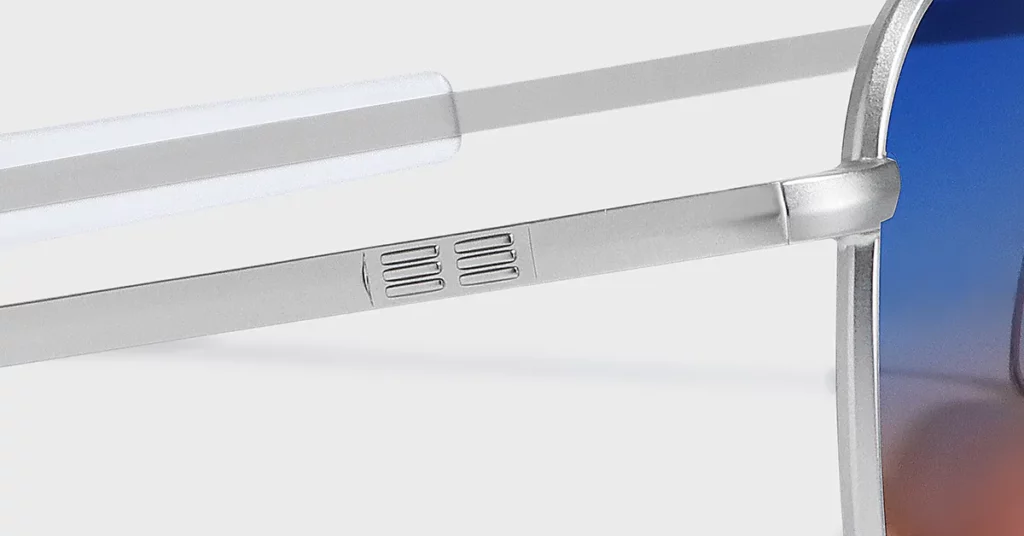
Lens Filter Categories (0-4) and Use Cases
The standard’s five filter categories create a universal language for lens tint performance. This classification allows you to match lens properties to specific consumer activities, which helps manage customer expectations and reduce liability.
Filter Category | Light Transmission | Description | Suitable Use Cases |
0 | 80-100% | Very light tint | Indoor use, overcast days |
1 | 43-80% | Light tint | Low sun exposure |
2 | 18-43% | Medium tint | General purpose, suitable for driving |
3 | 8-18% | Dark tint | Bright sun, beach, mountains |
4 | 3-8% | Very dark tint | Extreme glare, high altitudes |
The Bottom Line: Category 4 sunglasses transmit very little light and must be marked “not suitable for driving.” Failure to include this warning creates a significant safety and liability risk.
Guaranteeing Visual Clarity
Poor optical quality can cause eye strain and headaches. The standard sets precise limits on optical distortions to ensure sunglasses protect vision without compromising it.
- Spherical & Astigmatic Power: Limits on refractive power ensure clear, undistorted vision.
- Prismatic Power: Limits on prismatic deviation prevent the lenses from creating a disorienting prism effect that can lead to eye strain.
Ensuring Structural Integrity
Frame performance requirements ensure the sunglasses can withstand normal use.
- Impact Resistance: A minimum robustness test ensures the frame can retain the lenses upon impact.
- Bridge Deformation: The frame must resist deformation under stress to maintain its fit and function.
- Ignition Resistance: Materials must be resistant to ignition.
- Biocompatibility: Materials that contact the skin must be assessed for safety to prevent allergic reactions.
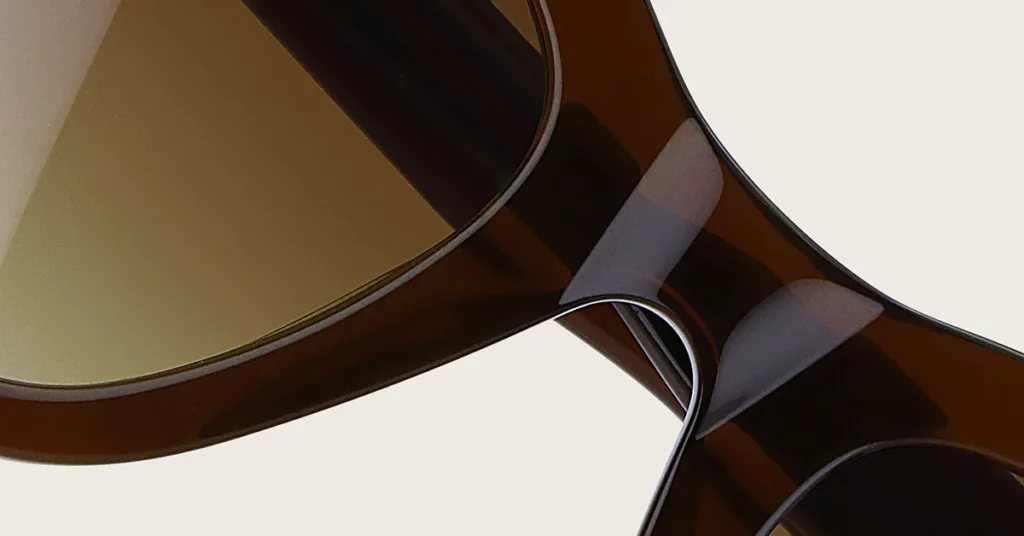
From Compliant Design to Commercial Success
A “global SKU” strategy, where one product meets multiple regional standards, is the most efficient path to market. This requires a deep analysis of regulatory overlaps and divergences to minimize development costs and maximize market access.
The Impact Resistance Challenge
The core design challenge for a global SKU is reconciling the different impact resistance tests required by the U.S. and EU. You must design to the highest standard to ensure universal compliance.
Attribute | FDA Drop Ball Test | ISO Minimum Robustness Test |
Test Object | 0.56 oz (16g) steel ball | 22mm diameter steel ball |
Drop Height | 50 inches (1.27m) | Varies (lower energy) |
Impact Energy | Higher | Lower |
Primary Goal | Prevent lens shattering | Ensure lens retention in frame |
The Bottom Line: A product that passes the FDA drop ball test will almost always pass the ISO minimum robustness test. Therefore, engineering for FDA compliance is the most effective strategy for creating a global product, as it covers the more stringent requirement.
Navigating Chemical Compliance with REACH and Prop 65
Chemical compliance is a major source of risk. You must actively manage restricted substances to avoid costly recalls and legal action.
- REACH (EU): This regulation restricts substances like heavy metals (lead, cadmium, nickel) and phthalates in plastics. You are responsible for ensuring every component in your supply chain is compliant.
- California Proposition 65: This law requires you to provide a warning label if your product contains any of over 900 listed chemicals, such as nickel in metal frames. The primary risk here is private litigation.
Best Practice: Implement a comprehensive chemical testing program that screens for both REACH and Prop 65 substances. This is the only way to de-risk your access to these critical markets.
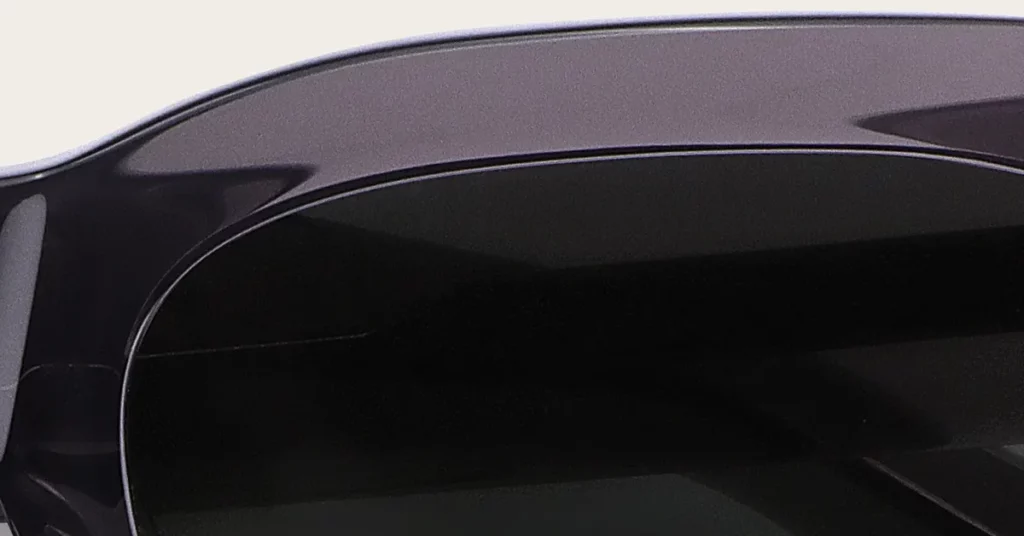
Embedding Compliance into the Product Development Lifecycle
Compliance should not be an afterthought; it must be engineered into the product from the material selection phase. This proactive approach is always cheaper and more effective than reactive testing and redesign.
Material Science as a Compliance Tool
Your choice of lens material can be a powerful compliance tool. Advanced materials offer inherent properties that meet or exceed key regulatory requirements, simplifying your path to market.
- Polycarbonate: This material’s primary advantage is its extreme impact resistance, allowing it to easily pass the FDA drop ball test. It also offers inherent UV protection up to 380nm, which reduces the need for additional lens coatings and lowers manufacturing costs.
- Trivex: Offers superior optical clarity (higher Abbe value) compared to polycarbonate while still meeting FDA impact standards. It also has better chemical resistance, enhancing long-term durability.
Prototyping and Pre-testing
You must treat prototype testing as an insurance policy against mass production failures. Investing in pre-testing allows you to verify your design and material choices before committing capital to tooling and inventory. This process identifies compliance gaps when they are cheapest to fix.
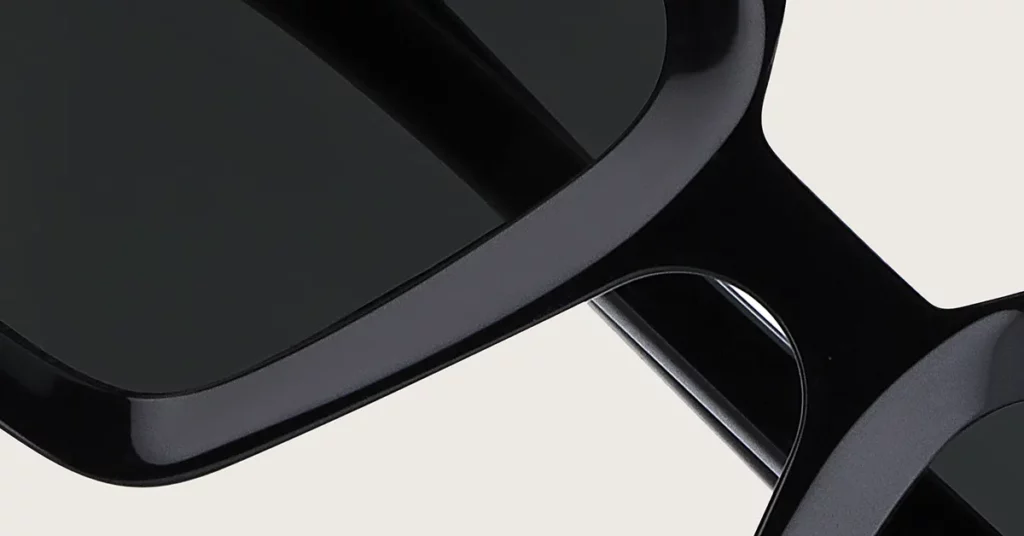
The Vetting Framework: Selecting a Compliant Manufacturer
Your choice of manufacturing partner is the single most important decision you will make in your compliance strategy. You must look beyond marketing claims and demand verifiable proof of capability.
The Hierarchy of Proof
Not all compliance documentation is created equal. You must understand the difference between a simple claim and independently verified proof.
- Level 1: Manufacturer’s Self-Declaration (DoC): This is the lowest level of assurance. The manufacturer simply states they are compliant, assuming all legal liability but offering no independent proof.
- Level 2: In-House QC Records: This demonstrates a more robust process. The factory provides its own internal batch testing records, such as drop ball test logs. Demand to see records of equipment calibration and operator training.
- Level 3: Accredited Third-Party Lab Reports: This provides strong, independent verification from an accredited lab like Intertek, SGS, or Bureau Veritas. These reports are unbiased and based on standardized, calibrated testing protocols.
- The Gold Standard: Certified Quality Management System (ISO 9001): An ISO 9001 certification shows the manufacturer has a systematic, audited process for maintaining quality and consistency. This is the highest level of assurance that compliance is a repeatable process, not a one-time event.
Due Diligence Checklist
- Demand Full Test Reports: Never accept a simple pass/fail summary. Request the full, unabridged test report from an accredited third-party lab. Scrutinize it for the specific standards used, the test conditions, and laboratory accreditation.
- Verify Traceability: A competent manufacturer must have a robust traceability system. Demand to see their lot numbering system and how they can trace a finished product back to its raw material batches via a Bill of Materials (BOM).
- Conduct On-Site Audits: You must physically inspect the factory. Verify that the testing equipment they claim to have (e.g., drop ball testers, spectrophotometers) actually exists, is calibrated, and is operated by trained personnel.
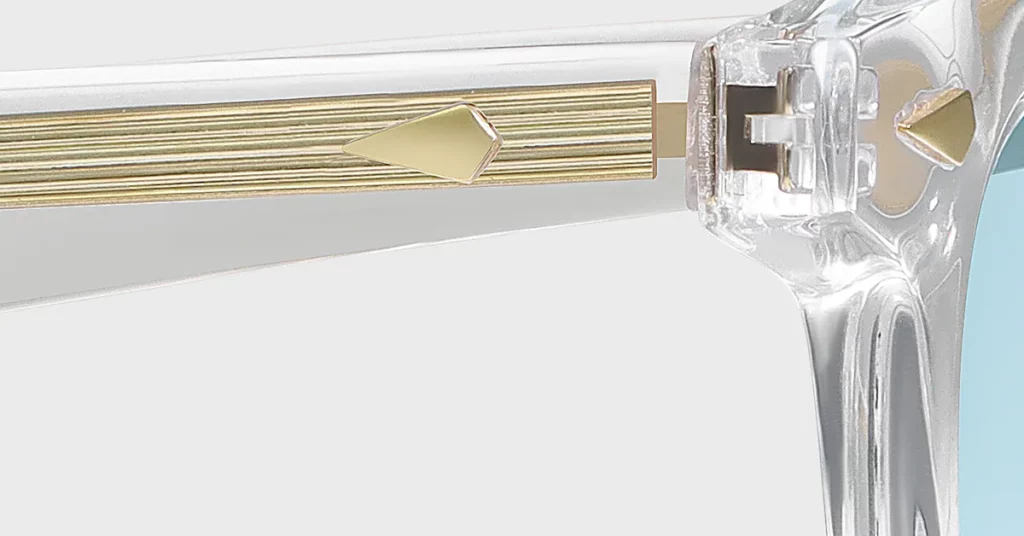
Conclusion
Mastering FDA, CE, and ISO standards transforms compliance from a cost center into a competitive weapon. This knowledge allows you to make strategic decisions about product design, material selection, and manufacturing partnerships that secure global market access. By building your product strategy on a foundation of verified compliance, you reduce risk, accelerate growth, and build the brand authority that justifies a premium price.
Frequently Asked Questions
1. Can a single sunglass model meet both FDA and CE rules?
Yes. You must design to the more stringent FDA drop ball test. Using materials like polycarbonate achieves this and will subsequently meet the less demanding ISO 12312-1 impact requirements for the CE mark.
2. What is the business difference between a DoC and a lab report?
A self-declared DoC is a manufacturer’s unverified claim, placing all liability on you. A third-party lab report provides independent, verifiable proof of compliance, which reduces your liability and is often required by major retailers.
3. What are the biggest chemical compliance risks for eyewear?
REACH in the EU and California’s Proposition 65 pose the greatest risks. The main concerns are restricted substances like lead, phthalates, and nickel. Supply chain contamination is the top threat, where one bad component batch can force a massive recall.
4. Does an ISO 12312-1 report guarantee FDA impact compliance?
No. The FDA drop ball test is a more difficult impact test than the minimum robustness test in ISO 12312-1. A product must be specifically tested and pass the FDA standard; ISO compliance alone is not sufficient proof.
5. How does fashion eyewear compliance differ from safety eyewear?
Fashion sunglasses fall under FDA Class I medical device rules and CE PPE Category I, requiring basic UV and impact protection. Safety eyewear must meet higher standards like ANSI Z87.1, which mandates significantly greater impact resistance and requires third-party certification.