A premium acetate frame is the result of a systematic process combining material science, precision engineering, and artisanal craftsmanship. The production method begins with rigorous material vetting, moves to CNC machining with +/- 0.1mm tolerances, and finishes with multi-stage tumbling and hand-finishing. Each step has technical competencies and quality controls that directly determine frame durability, aesthetic value, and your brand’s market power.
Step 1: The Strategic Foundation – Vetting Design & Materials
Your partner’s approach to design interpretation and material sourcing is the cornerstone of your collection. This foundation determines if your brand vision becomes a market-ready product that commands a premium price and earns customer loyalty. Your financial success begins here.
Evaluating the Design-to-Manufacturing Blueprint
The move from a design concept to a physical product demands a manufacturer who understands both your aesthetic vision and the unyielding constraints of physics. Premium acetate production requires partners who maintain design integrity while optimizing for manufacturability. This is not about cutting corners; it’s about engineering for excellence and profitability.
Best Practice: During the conceptual phase, your partner must provide technical feedback that prevents costly downstream revisions. This initial input is a key indicator of their strategic value beyond simple production.
CAD/CAM Capabilities for Precise Technical Specs
Modern acetate production depends on Computer-Aided Design (CAD) and Computer-Aided Manufacturing (CAM) for precision. Your partner must demonstrate mastery in converting 2D concepts into 3D CAD models with manufacturable specifications.
- The CAD process generates technical drawings specifying all dimensions, from lens grooves to temple curvatures. These specs must account for material shrinkage and manufacturing tolerances. A competent partner provides renderings that prove the design meets optical standards and wearer comfort.
- CAM programming dictates CNC machine execution. This involves optimizing tool paths and cutting speeds to minimize material waste while achieving a superior surface finish. Advanced CAM capabilities can cut production time by 15-20% and improve dimensional accuracy.
Key Metric: Demand CAD files that show tolerance specifications of +/- 0.1mm. The files must include documented revision tracking, which provides a clear audit trail for quality control.
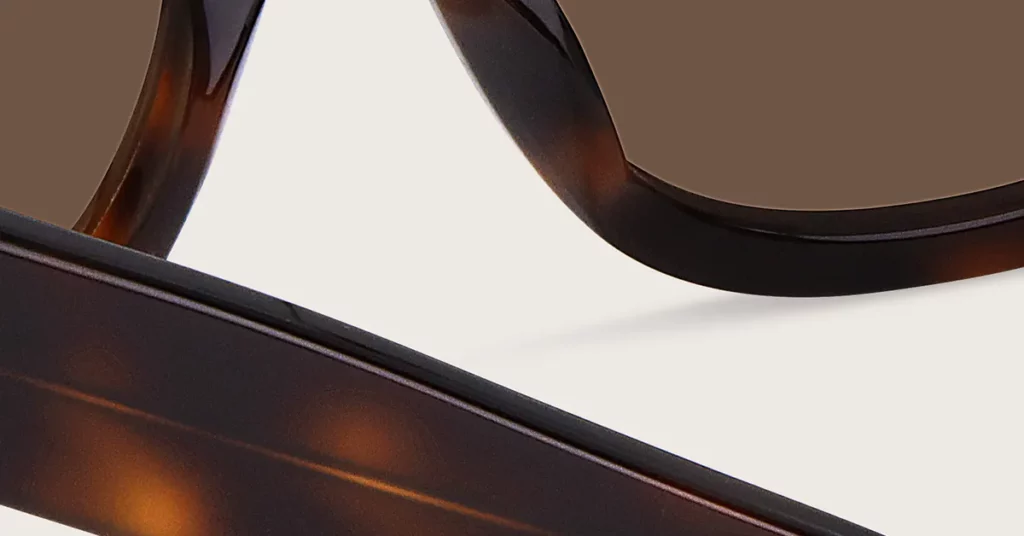
The Role of Physical Prototyping
Digital models cannot replicate the tactile experience of eyewear. Physical prototyping is the validation step where design intent meets real-world function. Premium manufacturers invest in creating multiple iterations before committing to production tooling, saving you from market failure.
This phase typically involves 3-5 iterations of each design to refine fit, weight distribution, and visual balance. Each prototype undergoes wearing trials to identify pressure points or imbalances. Advanced prototyping also includes stress testing to evaluate hinge durability and frame resilience, simulating months of wear in days.
Critical Warning: Partners who rush prototyping to “save” money are creating expensive future problems. Frames produced this way almost always require extensive and costly revisions during the main production run, destroying timelines and budgets.
Deconstructing the Foundational Material
Material selection is the single most important decision in acetate frame production. Your choice directly impacts product quality, durability, and your brand’s position in the market. Understanding the technical differences between acetate types is a prerequisite for smart sourcing.
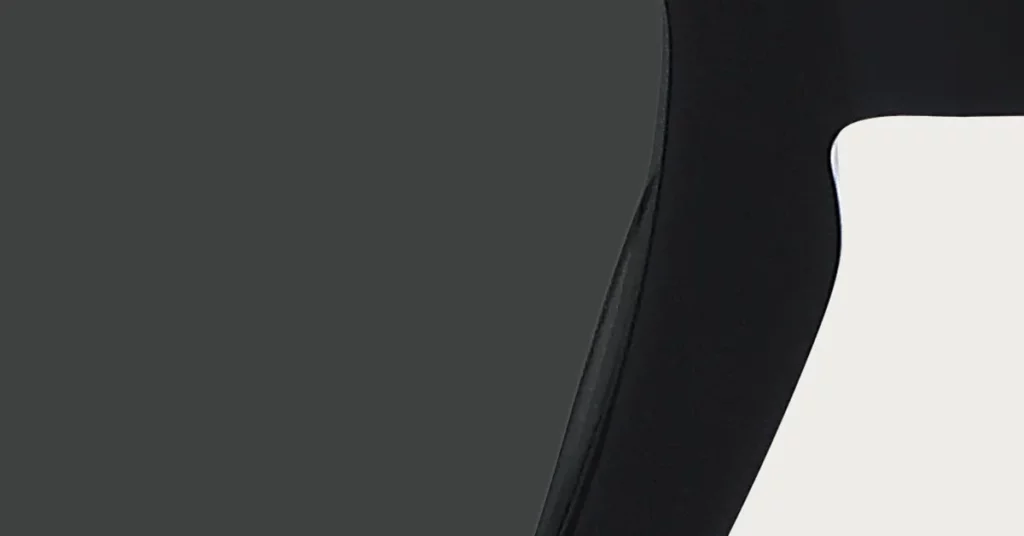
Comparative Analysis: Standard vs. Premium vs. Bio-Acetate
The acetate you choose dictates your market segment. Each material offers distinct properties that align with specific brand positions and pricing strategies. Your material is your message.
Attribute | Standard Acetate | Premium Italian Acetate | Sustainable Bio-Acetate |
Material | Petroleum-Based Plastic | Mazzucchelli Cellulose Acetate | Cotton & Wood Pulp Derived |
Cost Premium | Baseline | +40-60% | +25-35% |
Color & Pattern | Limited, Surface-Level | Excellent Depth, Complex Layers | Good Depth, Sustainable Story |
Adjustability | Basic | Superior | Good |
Market Position | Mass Market | Luxury / Premium | Conscious Premium |
The Bottom Line: Your material cost is an investment in your retail price. The 40-60% cost premium for Italian acetate is what enables the 80-120% retail price premium your brand will command.
Technical Evaluation of Acetate Sheets
A technical evaluation of acetate sheets requires a deep understanding of material science. The color depth, lamination, and curing of the raw material directly impact the final product’s quality and long-term durability.
- Color Depth: In premium acetate, color is not a coating; it’s structural. The block acetate method, an Italian specialty, involves compressing multiple colored layers into large blocks. This creates unique, complex patterns that run through the entire material thickness.
- Lamination Integrity: Acetate sheets must be cured with controlled heating and cooling cycles. This allows internal stresses to relax and maintains dimensional stability. Improper curing leads to warping, color bleeding, or delamination.
- Curing Time: Curing can take from several days to several weeks, depending on sheet thickness. Proper curing is a non-negotiable step that ensures volatile compounds are eliminated, preventing potential allergic reactions and guaranteeing long-term frame stability.
Definition: Block acetate is the Italian production method where colored acetate layers are compressed into large blocks before being sliced. This process is responsible for the superior color depth and unique patterns found in premium eyewear.
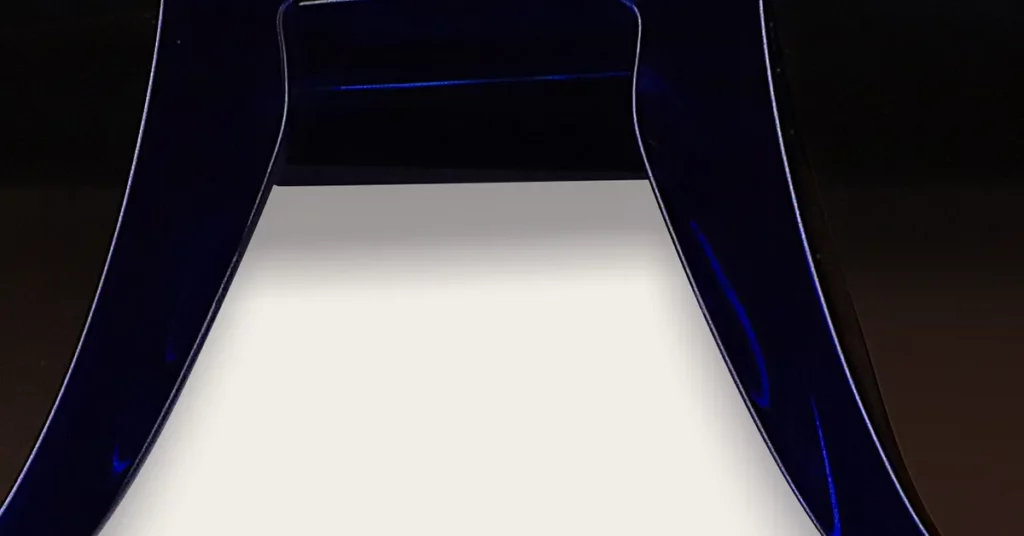
Steps 2-4: Core Manufacturing – Machining & Integration
This phase transforms raw acetate sheets into engineered frame components. It demands sophisticated 5-axis CNC equipment, technical expertise, and rigorous quality control to achieve the tight tolerances premium eyewear requires.
Vetting the CNC Milling Stage
CNC milling is the most technically demanding part of acetate production. It requires 5-axis machining capabilities and specialized tooling to handle the complex geometry of eyewear.
- Required Tolerances: Premium frames require dimensional tolerances of +/- 0.1mm. This precision is necessary for proper lens fit, hinge alignment, and overall geometric integrity.
- Cutting Speeds: Speeds are optimized based on acetate hardness. This is typically 8,000-12,000 RPM for roughing and 15,000-20,000 RPM for finishing passes. Incorrect speeds or feed rates cause heat buildup, which can melt the acetate.
- Surface Finish: The lens groove requires the finest finish (Ra 0.8-1.2) to prevent lens scratching. Exterior surfaces need a consistent finish (Ra 1.6-2.0) to ensure a uniform appearance after polishing.
Key Metric: Your manufacturer must monitor cutting tool life via piece count tracking. Tools must be replaced before wear patterns compromise dimensional accuracy or surface quality.
Frame Front & Temple Machining Analysis
The frame front and temples contain the most critical dimensions. They must be machined with absolute accuracy to ensure optical alignment and wearer comfort.
- Frame Front: The precision of the lens groove dictates lens retention. A deviation as small as 0.05mm can cause a lens to pop out. The bridge geometry must be precisely shaped to distribute weight evenly across the nose.
- Temples: The wire core channel is the most critical feature of the temple. This channel must be perfectly positioned to accept the metal reinforcement wire. An undersized channel means the wire cannot be fully inserted, which directly leads to temple failure.
Critical Warning: Inadequate wire core channel dimensions are a primary cause of temple breakage. This is not just a quality issue; it is a potential safety hazard for your customer.
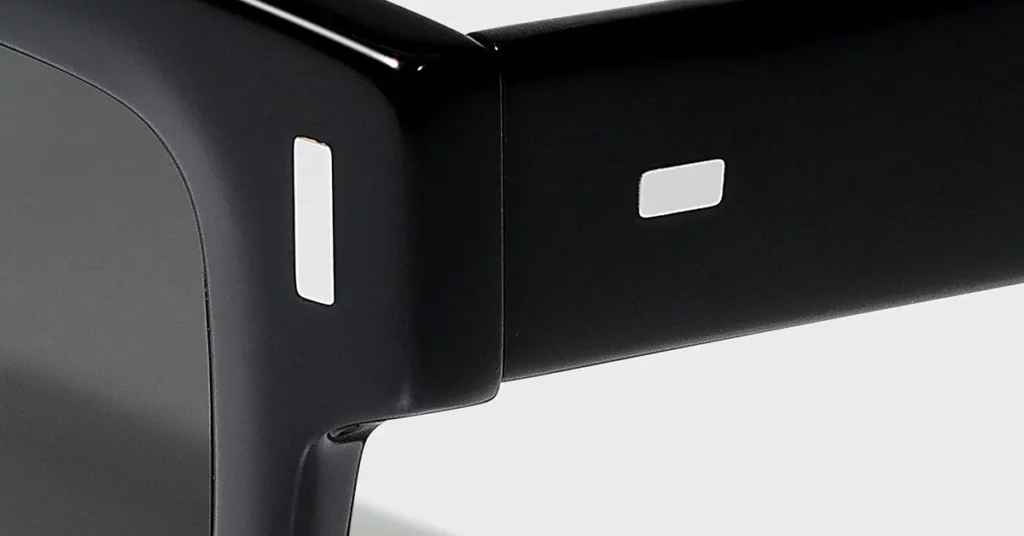
Auditing Component Integration
Component integration is where machined parts become a functional frame. This process requires specialized equipment and skilled operators to achieve the mechanical durability your brand promise relies on.
The Core-Shooting Process
Core-shooting is the process of inserting a metal wire reinforcement into an acetate temple using controlled heat and pressure. This creates the required strength and flexibility. Proper execution requires precise control over temperature (typically 80-120°C) and pressure (50-150 PSI) to ensure complete wire insertion and permanent adhesion.
Best Practice: Demand that your partner uses statistical process control for core-shooting. Monitoring temperature, pressure, and cycle time is the only way to maintain consistent adhesion quality and prevent delamination.
Hinge Evaluation Framework
Your hinge choice directly impacts frame durability, perceived quality, and your warranty budget. Understanding the trade-offs is a financial necessity.
Hinge Type | Strength | Durability | Aesthetics | Installation Complexity | Business Impact |
3-Barrel Riveted | High | Excellent | Good | Medium | Standard for quality frames. |
5-Barrel Riveted | Excellent | Superior | Good | Medium | Reduces warranty claims by 30-40%. |
3-Barrel Heat-Insert | Medium | Good | Excellent | High | Clean look, but lower durability. |
5-Barrel Heat-Insert | High | Excellent | Excellent | High | Premium choice for aesthetics & durability. |
The Bottom Line: Hinge selection is an insurance policy against warranty claims. A 5-barrel hinge provides a 30-40% longer service life than a 3-barrel version. While the initial component cost is higher, this investment is typically recouped within 12-18 months through a 25-35% reduction in hinge-related warranty claims.
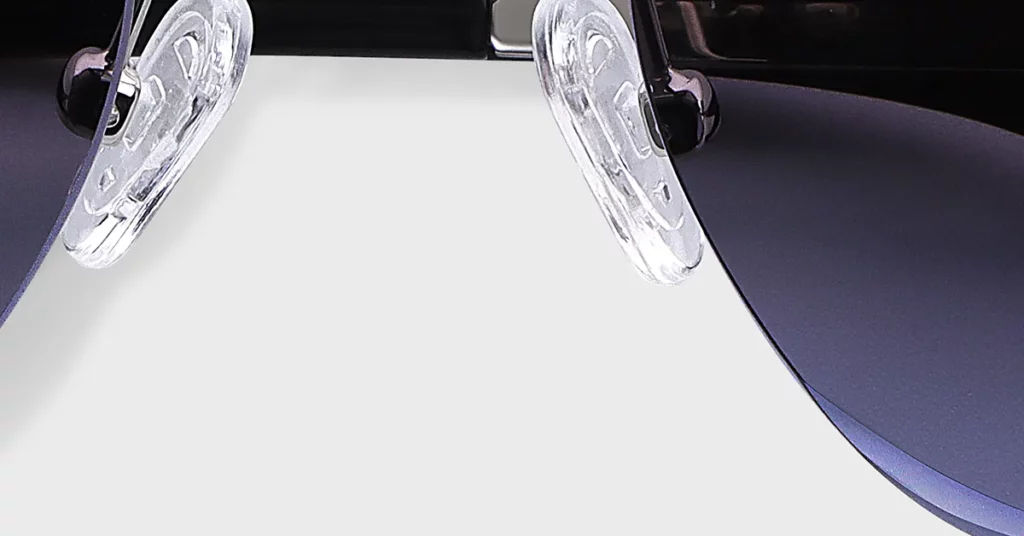
Steps 5-6: Mastering the Finish – Polishing & Hand-Crafting
The finishing phase transforms machined components into aesthetically refined frames that justify a premium price. This stage combines automated tumbling with skilled hand-crafting to achieve a flawless surface.
Deconstructing the Multi-Day Tumbling Process
Tumbling is the foundation of acetate finishing. It uses controlled abrasion over 72-120 hours to remove machining marks and develop a deep, lustrous surface. The process is a multi-stage affair:
- Rough Tumbling (12-24 hours): Uses large wood or ceramic chips to remove the primary CNC tool marks.
- Medium Tumbling (24-48 hours): Uses medium-sized wood chips to refine the surface texture and create a uniform appearance.
- Final Tumbling (24-48 hours): Uses fine wood chips or specialized polishing media to develop the smooth, reflective surface that enhances color depth.
Key Metric: An effective tumbling process targets a final surface roughness of Ra 0.8-1.2 μm. Demand to see profilometer reports that verify this level of finish quality.
Hand-Finishing: The Luxury Benchmark
Hand-finishing is where skilled craftspeople use a polishing wheel to address areas that automated tumbling cannot reach. This final refinement is what creates the flawless surface quality expected from a luxury product. This manual process is slower and more expensive, but it is a non-negotiable step for achieving a truly premium feel.
Pro Tip: Your partner should implement quality checkpoints every 50 frames during hand-polishing. This protocol maintains consistent standards and identifies process variations before they affect a large batch, protecting your investment.
Validating Ergonomic Shaping and Forming
Ergonomic shaping turns a geometrically correct frame into comfortable eyewear. This requires a deep understanding of facial anatomy and material behavior.
- Bridge “Bumping”: This is the controlled forming process that creates the 3D curvature of the bridge for optimal nose comfort. It requires precise heat application (60-80°C) and specialized tooling to create the shape without introducing stress into the acetate.
- Temple Bending & Pantoscopic Tilt: Adjusting the temple curve and the pantoscopic tilt (the angle of the lens plane) is vital for correct optical alignment. An error of just 2-3 degrees can cause noticeable visual distortion and discomfort for the wearer.
Best Practice: Your partner must use documented processes and quality control systems, like coordinate measuring machines (CMM), to maintain custom curvatures consistently across an entire production run. This is a key differentiator between premium and commodity manufacturing.
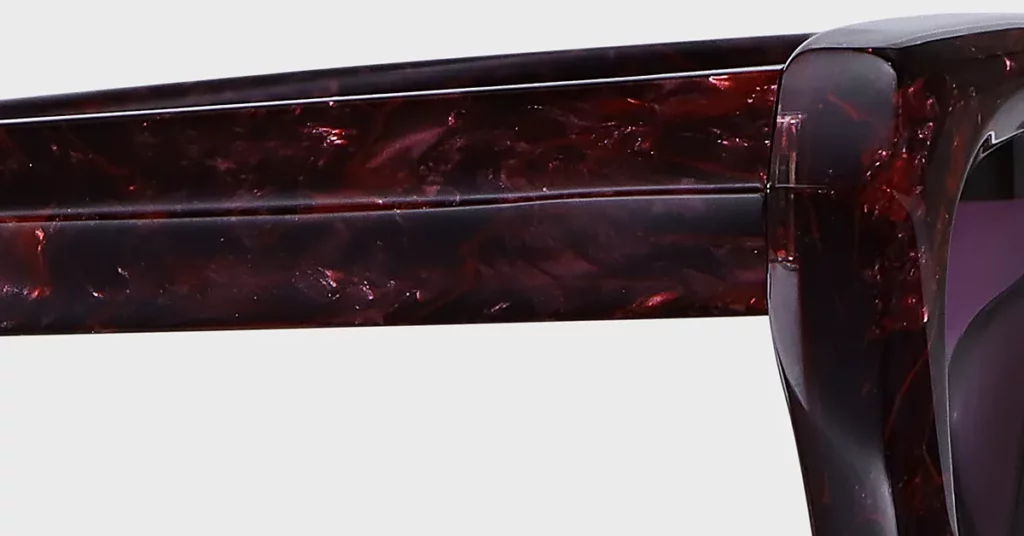
Step 7: The Partnership Litmus Test – Final Assembly & QA
Final assembly is the ultimate test of a manufacturer’s capability. This is where the precision of every previous step becomes evident. Inconsistent fit and function at this stage is a clear signal of a systemic failure in the production process.
Analyzing the Final Assembly Stage
Final assembly demands precise coordination. Hinge alignment, temple attachment, and screw quality must be perfect for smooth, long-term functionality.
- Hinge Alignment: Must be verified with specialized fixtures to a tolerance of +/- 0.05mm. Misaligned hinges create binding and premature wear, leading to customer complaints and returns.
- Lens Insertion: Requires careful technique to prevent frame warping. Excessive insertion force can create micro-cracks in the acetate that are not immediately visible but will cause eventual frame failure.
Key Metric: A quality hinge system should demonstrate smooth action through 10,000 cycles without binding. This represents approximately 5-7 years of normal use and is a benchmark for long-term durability.
Implementing a Rigorous End-to-End QC Program
A comprehensive QC program identifies issues early and drives process improvement. Your partner’s commitment to QC is a direct reflection of their commitment to your brand’s quality.
Defining Critical Inspection Checkpoints
Inspection checkpoints must be positioned strategically to catch defects before they become expensive to fix. Your partner should be able to provide detailed reports from these checkpoints:
- Frame Alignment: Verifying geometric accuracy and optical alignment.
- Material Imperfections: Using trained inspectors to identify blemishes, inclusions, or stress points.
- Polish Consistency: Evaluating surface smoothness, gloss level, and color uniformity.
Best Practice: A professional QC setup uses standardized lighting (5000K-6500K color temperature), magnification, and calibrated calipers. This removes subjectivity from the inspection process and ensures consistent, repeatable measurements.
Demanding Actionable QC Reports
QC reports are not for filing away; they are tools for strategic management. Demand reports that provide actionable data.
The Bottom Line: Reports must contain quantitative measurements, trend analysis, and clear traceability. This data allows you to hold your partner accountable, track performance over time, and trace any quality issue back to its root cause for immediate correction. This is the foundation of a true partnership.
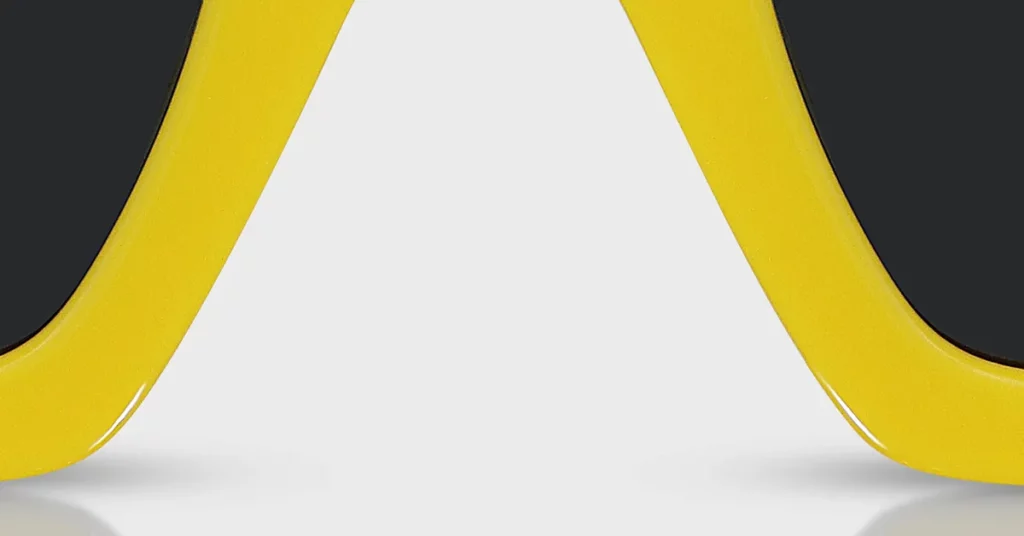
The B2B Payoff: Translating Production Excellence into Market Success
Understanding the technical details of acetate production empowers you to make strategic business decisions. This knowledge transforms your manufacturing partnership from a cost center into a profit driver.
Calculating the ROI of Premium Manufacturing
The higher costs of premium manufacturing must translate into market value. The investments in superior materials and craftsmanship directly justify a premium retail price and build the brand equity that drives long-term growth.
Cost Component | Standard Production % of Total Cost | Premium Production % of Total Cost | Direct Cost Increase | Retail Price Impact |
Materials | 5-7% | 8-12% | +3-5% | +40-60% |
Labor | 15-20% | 18-25% | +3-5% | +25-35% |
Quality Control | 2-3% | 4-6% | +2-3% | +15-25% |
Total Impact | – | – | +8-13% | +80-120% |
Differentiating from Injection Molding
Injection molding is the primary low-cost alternative. Communicating the tangible differences is key to defending your premium price point. Premium acetate offers:
- Superior Durability: Acetate has better impact resistance and flexibility, whereas injection-molded frames can become brittle and suffer from stress cracking.
- Unmatched Color Richness: Acetate’s color is structural, running through the material. Injection molding relies on surface coatings that can chip and fade.
- A Premium Hand-Feel: Acetate has a satisfying weight and warmth that immediately communicates quality.
For Example: A premium acetate frame costing $25 to manufacture can command a $200-$300 retail price. A comparable injection-molded frame costing $8 to produce typically retails for only $50-$80. The market clearly recognizes and rewards the value of superior production.
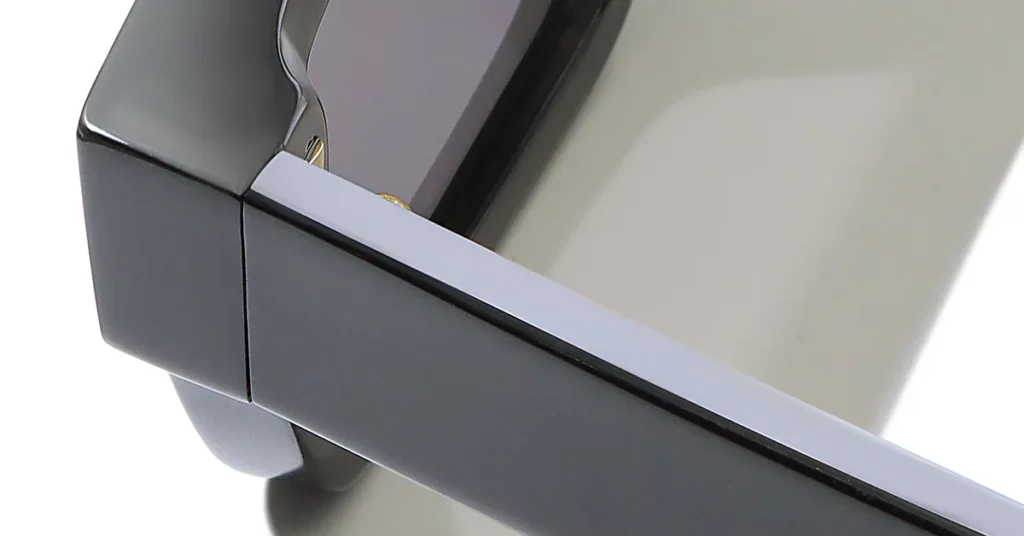
Conclusion
This 7-step analysis provides the technical framework for vetting manufacturing partners. By understanding each stage, you can verify quality claims and establish the production standards your brand requires for market leadership.
Kssmi’s transparent methodology is our commitment to excellence and the quality assurance your brand needs to compete and win in the premium market. To see how our process can elevate your collection, contact our technical team to schedule a manufacturing consultation.
Frequently Asked Questions
1. How does acetate curing time impact long-term stability?
Proper curing at 60°C for at least one week allows internal stresses to relax and volatile compounds to evaporate. This process is fundamental for preventing warping and ensuring the frame maintains its shape over its lifetime. Insufficient curing is a primary cause of long-term dimensional instability.
2. What is the performance difference between a 3-barrel and 5-barrel hinge?
A 5-barrel hinge offers a 30-40% longer service life due to increased bearing surface area, which improves load distribution and reduces wear. This translates to a smoother, more substantial feel and a significant reduction in warranty claims related to hinge failure.
3. What is the CNC machining tolerance for a luxury-grade frame front?
The benchmark for a luxury frame is +/- 0.1mm across all critical dimensions. The lens groove is even more demanding, requiring tolerances below 0.05mm to guarantee secure lens retention and prevent optical distortion.
4. How does bio-acetate affect color range and polishing?
Bio-acetate offers a slightly more limited color palette compared to traditional acetate, particularly for deep, saturated colors. The polishing process may also require modified compounds or longer tumbling times to achieve an equivalent high-gloss finish due to different material properties.
5. What objective tests can verify metal core adhesion in a temple?
Beyond visual checks, you should demand quantitative data. Pull-out force testing, where premium frames should withstand 50-100 pounds of force, is a standard mechanical test. Thermal cycling and ultrasonic inspection are also used to verify bond integrity.